Размеры шеек коленвала
Коленчатый вал (коленвал) — важный узел в составе кривошипно-шатунного механизма автомобиля. Его функция заключается в том, чтобы воспринимать возвратно-поступательное движение поршней и преобразовывать его в крутящий момент, обеспечивая таким образом плавную работу двигателя. Конструктивно состоит из нескольких коренных и шатунных шеек, соединенных между собой щеками. По мере износа вал перешлифовывают на ремонтные размеры, что соответственно меняет и размеры шеек коленвала. Обычно предусматривается до 6 ремонтных размеров, советские стандарты допускали 8 для ряда моделей.
Когда требуются ремонтные размеры коленвалов
Место перехода от коренной или шатунной шейки к щеке испытывает наибольшие нагрузки в конструкции коленвала, а потому износ в этом месте наиболее велик. По мере эксплуатации мотора на шейках появляются задиры и трещины, которые приводят к нарушению геометрии вала и должны быть устранены как можно скорее. Устраняются они шлифованием. Для того чтобы двигатель работал сбалансированно и без лишней вибрации, новые размеры коренных и шатунных шеек коленвала должны быть точно подогнаны к валу и друг другу. Делается это при помощи специальных вкладышей. Для удобства автомехаников диаметры шеек и толщина вкладышей были стандартизированы для каждой модели автомобиля.
Таким образом, ремонтные размеры требуются при каждой шлифовке коленвала. Определяются они в зависимости от метода обработки вала. В ходе производства каждый вал проходит несколько этапов закалки, повышающих прочность и износостойкость его поверхности. Чаще всего используется термическая обработка, но в ряде случаев для усиления прочности воздействие высоких и низких температур сочетают с химическим (закалка ТВЧ, азотирование, закалка поверхностного слоя). В результате достигается достаточная глубина закалённого слоя, чтобы шейки вала можно было шлифовать 4–6 раз без потери рабочих качеств вала.
Важно знать, что валы, закаленные методом азотирования, не подлежат шлифовке.
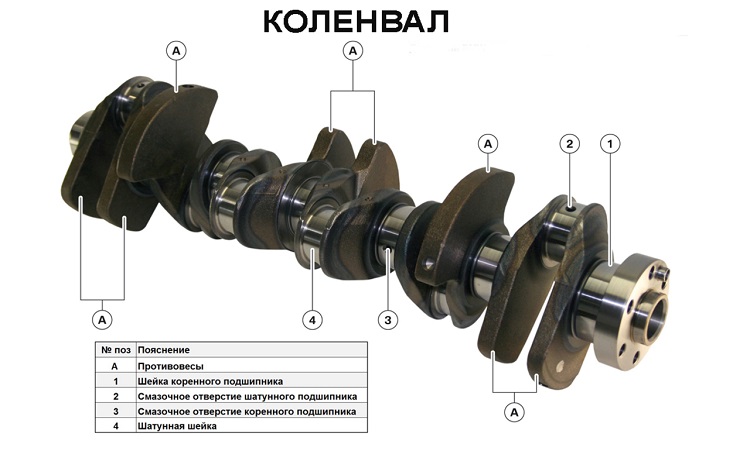
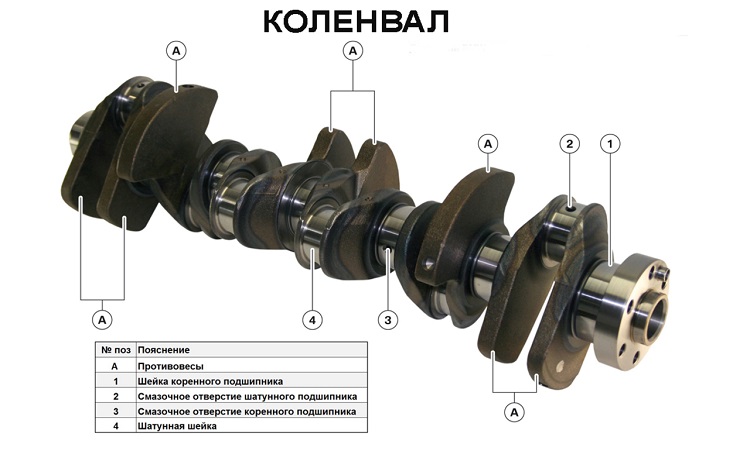
Образец коленвала
Конструкция коленвала:
- Коренная шейка — опорная часть вала. Находится в картере двигателя и опирается на коренной подшипник.
- Шатунная шейка соединяет вал с шатунами и одновременно обеспечивает поступление к ним смазки через специальные каналы.
- Щёки — детали, соединяющие коренные и шатунные шейки.
- Передняя выходная часть вала или носок — место крепления зубчатого колеса или шкива отбора мощности для привода ГРМ.
- Задняя выходная часть вала или хвостовик — место крепления маховика или шестернёй отбора мощности.
- Противовесы — конструктивно являются продолжением щек и снимают часть нагрузки с коренных подшипников.
Как узнать размеры коленвалов
Существуют специальные таблицы, где можно узнать размеры коленвалов для конкретной модели автомобиля или техники. Такие таблицы есть для всех видов транспортных и технических средств, на которых установлен двигатель внутреннего сгорания. Размеры вкладышей, имеющихся в продаже, соответствуют этим размерам.
Например, для Opel Kadett 1,3S стандартные размеры коренных шеек составляют 54,972–54,985 мм, при шлифовке на глубину 0,25 мм – 54,722 – 54,735 мм, при шлифовке на 0,5 мм – 54,472 – 54,485. Размеры шатунных шеек, соответственно, составляют 42,971 – 42,987 в стандартном (нулевом) варианте, 42,721 – 42,737 при шлифовке на 0,25 мм и 42,471 – 42,787 при глубине обработки 0,5 мм. Для автомобиля ВАЗ-2108 стандартный диаметр составит уже 50,779–50,819 мм, а ремонтных размеров предусмотрено четыре: 50,549–50,569, 50,229–50,319, 50,049–50,069 и 49,799–49,819.
Как правило, при первом ремонте шейку шлифуют на глубину около 0,25 мм. Следующие размеры располагаются друг от друга на таком же расстоянии: 0,5, 0,75 и 1 мм. Для ряда моделей также возможны шаги в 0,125 мм. Таблицы допускают шлифовку ещё на два размера, 1,25 и 1,5 мм, однако такая обработка чревата разрушения вала в процессе работы. По этой причине в магазинах размеры вкладышей 1,25 и 1,5 представлены редко. При значительном износе иногда перешлифовывают «через размер», т. е. уменьшают диаметр сразу на два размера.
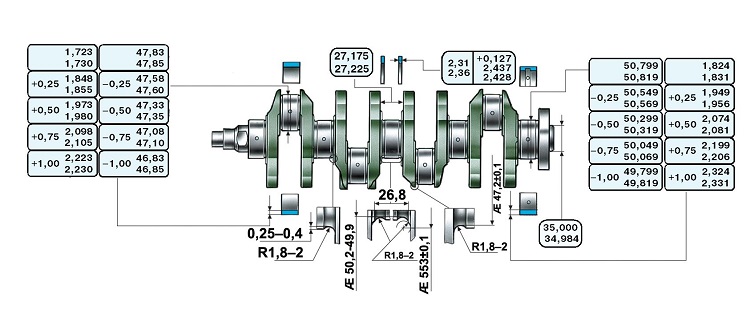
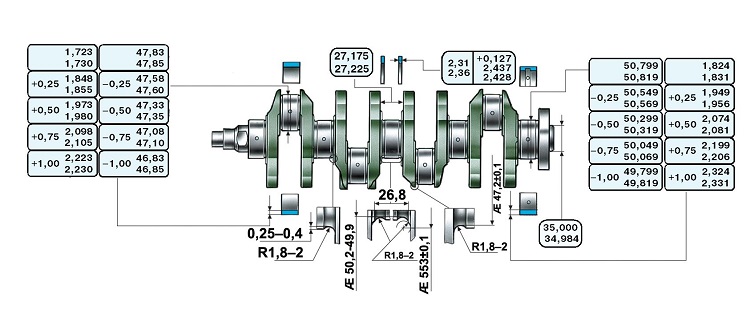
Размеры шеек на ВАЗ
Ремонт коленчатых валов
Шлифовка коленвала выполняется на вращающемся наждачным круге. В процессе работы вал поворачивают вокруг осей базирования то коренных, то шатунных шеек. Также необходимо следить за соблюдением межцентрового состояния и крайне бережно отнестись к сохранению форме галтелей, иначе ремонт может только ускорить разрушение коленчатого вала.
После шлифовки вал необходимо динамически отбалансировать в сборе с маховиком, чтобы избежать вибрации в отремонтированном двигателе. Однако на практике это условие редко выполняется, особенно при индивидуальном ремонте.
В некоторых случаях устранить повреждения шеек шлифованием невозможно. Тогда можно рассмотреть вариант наплавке или напыления (в том числе — плазменного) с последующим шлифованием под нулевой (номинальный) размер. В зависимости от наплавляемого материала прочность шейки может даже повыситься по сравнению с заводскими значениями. На финальной стадии обработки шейки полируют и подвергают финишированию до получения оптимальной степени шероховатости.
Важно учитывать, что размеры шеек одного типа обязательно должны совпадать. Разные типы же могут иметь разные диаметры. Например, коренные могут быть второго ремонтного размера, а шатунные – третьего. Исключение – ситуации полевого ремонта, при котором шейки могут вообще не иметь стандартного ремонтного размера.
Также необходимо отметить, что специфика нагрузок, приходящихся на коленвал, часто вызывает его поломку. Чаще всего это случается из-за увеличения зазоров с вкладышем, что влечет за собой ухудшение смазки. Сломанный коленвал не ремонтопригоден и подлежит замене.
Заключение
Шейка коленвала испытывает основные нагрузки при работе двигателя, поэтому состояние этой детали должно регулярно проверяться. Ее повышенный износ приводит к появлению дополнительных вибраций в двигателе и может, в конечном счете, вызвать поломку коленвала. При должном опыте и наличии оборудования можно выполнить шлифовку самостоятельно, однако большинство владельцев легковых машин предпочитает поручить эту работу профессионалам.
Вконтакте
Google+
В этом разделе мы приведем две таблицы соответствия диаметров шеек коленвалов.
Диаметр коренных шеек коленвалов.
МАРКА ДВИГАТЕЛЯ |
Номинальные размеры |
Ремонтные размеры |
||||
Н1 |
Н2 |
Р1 |
Р2 |
Р3 |
Р4 |
|
А-01 |
105,000 |
104,75-0,023 |
104,500 |
104,250 |
104,000 |
103,800 |
А-41 |
105,000 |
104,75-0,02; -0,043 |
104,500 |
104,250 |
104,000 |
103,800 |
СМД-18 |
92,250 |
92-0,015 |
91,500 |
91,000 |
90,500 |
90,000 |
СМД-20 |
92,250 |
92-0,015 |
91,500 |
91,000 |
90,500 |
90,000 |
СМД-22 |
92,250 |
92-0,015 |
91,500 |
91,000 |
90,500 |
90,000 |
СМД-31 |
92,250 |
92-0,015 |
91,500 |
91,000 |
90,500 |
90,000 |
СМД-60 |
92,250 |
92-0,015 |
91,500 |
91,000 |
90,500 |
90,000 |
Д-21 |
70,250 |
70-0,065; -0,085 |
69,500 |
69,000 |
68,500 |
68,000 |
Д-65 |
85,250 |
85-0,08; -0,1 |
84,500 |
84,000 |
83,500 |
83,000 |
Д-108 |
95,210 |
94,96-0,023 |
94,460 |
93,960 |
93,460 |
92,960 |
Д-144 |
70,250 |
70-0,065; -0,085 |
69,500 |
69,000 |
68,500 |
68,000 |
Д-160 |
95,210 |
94,96-0,023 |
94,460 |
93,960 |
93,460 |
92,960 |
Д-240 |
75,250 |
75-0,08; -0,95 |
74,500 |
74,000 |
73,500 |
73,000 |
ЯМЗ-236 |
— |
110-0,015 |
109,750 |
109,500 |
109,250 |
109,000 |
ЯМЗ-238 |
— |
110-0,015 |
109,750 |
109,500 |
109,250 |
109,000 |
Диаметр шатунных шеек коленвалов.
МАРКА ДВИГАТЕЛЯ |
Номинальные размеры |
Ремонтные размеры |
||||
Н1 |
Н2 |
Р1 |
Р2 |
Р3 |
|
|
А-01 |
88,000 |
87,75-0,023 |
87,500 |
87,250 |
87,000 |
86,750 |
А-41 |
88,000 |
87,75-0,023 |
87,500 |
87,250 |
87,000 |
86,750 |
СМД-18 |
78,250 |
78-0,095; -0,11 |
77,250 |
76,500 |
75,750 |
75,000 |
СМД-20 |
78,250 |
78-0,095; -0,11 |
77,250 |
76,500 |
75,750 |
75,000 |
СМД-22 |
78,250 |
78-0,095; -0,11 |
77,250 |
76,500 |
75,750 |
75,000 |
СМД-31 |
78,250 |
78-0,095; -0,11 |
77,250 |
76,500 |
75,750 |
75,000 |
СМД-60 |
85,250 |
85-0,015 |
84,500 |
84,000 |
83,500 |
83,000 |
Д-21 |
65,250 |
65-0,06; -0,08 |
64,500 |
64,000 |
63,500 |
63,000 |
Д-65 |
75,250 |
75-0,075 |
74,250 |
73,500 |
72,750 |
72,000 |
Д-108 |
92,210 |
91,96-0,023 |
91,210 |
90,460 |
89,710 |
88,960 |
Д-144 |
65,250 |
65-0,06; -0,08 |
64,500 |
64,000 |
63,500 |
63,000 |
Д-160 |
92,210 |
91,96-0,023 |
91,210 |
90,460 |
89,710 |
88,960 |
Д-240 |
68,250 |
68-0,075; -0,09 |
67,500 |
67,000 |
66,500 |
66,000 |
ЯМЗ-238 |
— |
88-0,015 |
87,750 |
87,500 |
87,250 |
87,000 |
СПОСОБ РЕМОНТНЫХ РАМЕРОВ
Определение ремонтных размеров шеек вала
При восстановлении вала способом ремонтных размеров следует определить ремонтные размеры шеек вала. При этом следует иметь в виду, что для подавляющего большинства двигателей, выпускаемых не менее пяти лет, можно найти вкладыши подшипников коленчатого вала с ремонтным уменьшением 0,25 и 0,50 мм. Для более старых двигателей часто имеются ремонтные размеры 0,75 мм, реже — 1,0 мм. Вкладыши следующих ремонтных размеров (1,25 и 1,50) встречаются редко. Для относительно новых двигателей вкладыши некоторых ремонтных размеров (обычно 0,25 и 0,50 мм) могут поставляться в запасные части от фирм-производителей автомобилей.
Перед определением ремонтного размера шеек коленчатого вала конкретного двигателя желательно располагать информацией о том, какие ремонтные вкладыши существуют и могут быть приобретены. Поэтому, например, не следует шлифовать вал в какой-либо ремонтный размер до момента получения (приобретения) необходимых вкладышей.
Учитывая, что все способы восстановления коленчатых валов уменьшают надежность их работы, желательно шлифовать вал в один из существующих ремонтных размеров, даже если этот размер соответствует последним ремонтам — 0,75 мм, 1,0 мм и более. К восстановлению шеек следует прибегать только при таких износах, когда последний ремонтный размер уже не проходит, а другого (в том числе, нового) вала приобрести не удается.
Зазор в подшипниках — величина, наиболее сильно влияющая на весь результат ремонта. Так, при зазоре 0,07+0,09 мм увеличивается шум двигателя, может упасть давление масла, что снизит ресурс. В то же время: зазор менее 0,03 мм становится опасен задирами и заклиниванием подшипника. Кроме того, меньший зазор требует , точности обработки постели, в то время как после подготовительной работы и, особенно, после непродолжительного и прогрева, геометрия постели уже не будет идеальной. Вследствие этого не следует стремиться к очень малым зазорам.
Измерение сопряженных деталей
Другой способ определения ремонтного размера предполагает последовательное измерение сопряженных деталей. Измеряется диаметр постели нутромером. Затем с помощью микрометра и шарика подшипника определяется толщина вкладыша. Измерения толщины вкладыша выполняются ближе к середине. следует учитывать отклонения формы постёли и зазор нигде не должен быть меньше 0,03 мм.
Следует отметить, что при измерениях постелей подшипников нередко оказывается, что их размер превышает уже заданный в литературе максимальный на 0,02 мм. Для шатунов это может быть исправлено обработкой отверстия постели в то же время как обработка постелей коренных вкладышей без специализированного оборудования проблематична. Небольшая их деформация, может быть компенсирована соответствующим незначительным увеличением диаметра вала. В любом случае все измененения размеров должны выполняться только после тщательных измерений, чтобы избежать ошибок, приводящих к недопустимому уменьшению зазоров в подшипниках.
Для сильно изношенных валов (износ шеек более 0,10-0,15 мм) определение ремонтного уменьшения диаметра шеек имеет особенности. Если вал не деформирован или правился, то основное внимание должно быть уделено шатунным шейкам. Так, максимально возможный ремонтный диаметр зависит от износа и овальности шейки. Практика показывает, что сильно изношенные шейки всегда овальны, причем максимальный износ наблюдается в направлении, близком к радиусу кривошипа. Например , максимальный износ шейки 0,15 мм, а овальность 0,1 мм то шейка вала пройдет в ремонтное уменьшение 025 мм. Биение коренных шеек вала еще больше усложняет подбор ремонтных размеров для шатунных шеек, исходя из условия сохранения хода поршня. Кроме того, после длительной эксплуатации двигателя и, особенно, серьезных повреждений шатунных шеек вал может иметь остаточное скручивание, когда, например, оси попарно расположенных шатунных шеек не совпадают. Чем сильнее износ и эллипсность шатунных шеек и чем меньше припуск на шлифование, тем, очевидно, сложнее обеспечить равенство радиусов кривошипа и общую ось парных шеек. На практике эти требования часто удается выполнить только при неоправданно больших ремонтных уменьшениях диаметров, а в некоторых случаях не удается вообще.
При сильном износе шатунной шейки и минимальном припуске на шлифование нередко приходится переходить на новую ось шейки, смещенную относительно старой на меньший радиус на величину, близкую к половине эллипса .
Обычно эта величина не превышает 0,1-0,3 мм, что является допустимым для всех типов двигателей легковых автомобилей (включая дизельные). Смещение более 0,3-0,5 мм может быть нежелательно для дизелей, это вызывает заметное снижение степени сжатия. Поэтому во всех случаях, когда обеспечить одинаковые радиусы кривошипов невозможно, следует стремиться к минимальной их разнице.
Вследствие деформации вала происходит увод осей шатунных шеек на различное расстояние от оси вращения вала. В результате деформации вала оси крайних шатунных шеек слабо отклоняются от своих прежних радиусов, в то время как оси средних шеек переходят на новые радиусы вращения (рисунок 3.3.19), если эти шейки находятся в плоскости деформации вала или рядом с ней (±30-40°). Шатунные шейки, расположенные в плоскостях, перпендикулярных плоскости деформации вала, смещаются в окружном направлении.
Рисунок 3.3.19 — Переход шатунных шеек на новые радиусы вращения при деформации вала:
а — деформированный вал; б — шейка имеет радиус вращения больше номинального.
На практике наиболее часто встречается случай, когда вал максимально деформируется по наиболее изношенной шейке, при этом направление биения коренных шеек получается к шатунной шейке (сжатие щек вала). Тогда происходит взаимная частичная компенсация износа и биения, в результате чего ремонтный диаметр можно сделать несколько больше.
Элементарный расчет показывает, что даже при не очень большом повреждении шатунной шейки из-за разрушения шатунного подшипника использовать ремонтное уменьшение -0,25 мм оказывается проблематично. Однако при оценке ремонтного уменьшения диаметров шеек необходимо ориентироваться в первую очередь на минимальный съем металла, а условия равенства радиусов кривошипов или общая ось попарно расположенных шеек второстепенны, но весьма желательны, особенно с точки зрения уравновешенности вала.
Если деформированный вал не правится, то часто наблюдается следующая картина. После разрушения крайнего шатунного подшипника образуется деформация вала у этой шейки в плоскости вала. Поскольку износ шейки имеет односторонний характер (сверху), он частично компенсируется биением. В то же время биение средних шеек может оказаться таким, что уже именно они будут определять ремонтное уменьшение размера. У валов шести и восьмицилиндровых двигателей наблюдается более сложная картина, поскольку их шатунные шейки не лежат в одной плоскости. Таким образом, ремонт деформированных валов без применения правки представляет собой достаточно сложную техническую задачу.
В зависимости от деформации (биения) вала способы ремонта будут следующими:
1)биение до 0,08-^0,10 мм — традиционный ремонт — шлифование всех шеек в ремонтный размер 0,25 или 0,50 мм, возможно исправление передней центровой фаски; биение 0,10-0,20 мм — шлифование в ремонтный размер 0,25+0,50 мм, возможна наварка (наплавка) хвостовика и шлифовка от новой базы, не исключена необходимость шлифования торцевых поверхностей вала, балансировка;
2)биение 0,20-0,40 мм и более аналогично, но ремонтный размер шеек вала -0,50 мм или больше, возможна наварка (наплавка) коренных шеек с биением более 0,40 мм, обязательны наварка хвостовика, шлифование торцевых поверхностей, балансировка.
У многих двигателей на коленчатых валах применяются фланцевые коренные вкладыши, выполненные за одно целое с упорными полукольцами. В ремонт такие вкладыши нередко поставляются с увеличенным расстоянием между торцами (для некоторых двигателей есть варианты как с увеличенной, так и со стандартной шириной), что предполагает шлифование торцевых поверхностей соответствующей коренной шейки вала. Обычно увеличение размера между торцами в два раза меньше, чем уменьшение диаметра, например, для вкладышей 0,25 мм торцевой размер увеличивается на 0,10-0,15 мм, а для 0,5 мм — на 0,20-0,25 мм.
Для двигателей с упорными полукольцами, выполненными отдельно от коренных вкладышей, упорные полукольца не входят в ремонтный комплект и должны быть заказаны отдельно. Для некоторых двигателей поставляются также упорные полукольца увеличенной толщины.
Ремонтное увеличение толщины упорных подшипников обеспечивает возможность исправления биения, кругов; скол и царапин на опорных поверхностях вала при его ремонте. В практике ремонта встречаются ситуации очень большого износа задней поверхности упорного подшипника коленчатого вала (более 0,8-1,0 мм). Обычно это является следствием остаточной смазки при сильной нагрузке на упорный подшипник со стороны сцепления. Одним из немногих возможных способов ремонта вала с таким повреждением является растачивание торца на токарном станке. После токарной обработки упорная поверхность полируется. Далее в расточку вставляются дополнительные полукольца после чего вал с полукольцами устанавливается в блок. В данном варианте ремонта дополнительные «плавающие» полукольца позволяют использовать обычные вкладыши с фланцами или двойные стандартной толщины полукольца на расточенном упорном торце коленчатого вала, не прибегая к специальным нестандартным полукольцам увеличенной толщины.
Рисунок 3.3.20 — Конструкция ремонтного упорного подшипника коленчатого вала:
1— дополнительные полукольца, установленные в расточку на поврежденном торце коленчатого вала;2— штатный вкладыш с упорными
полукольцами
Рисунок 3.3.21 — Растачивание поврежденной упорной поверхности коленчатого вала
Чтобы исключить или максимально ограничить деформацию вала после ремонта, рекомендуются следующие операции:
1.Предварительная термообработка перед шлифованием выдержка при 180°С в течение 3-4 часов с медленным охлаждением.
2.Шлифование коренных шеек только после шлифовании шатунных.
3.Термообработка после шлифования шатунных шеек перед шлифованием коренных.
Очевидно, выполнение подобных операций сопряжено с большими затратами времени и необходимостью применения специального термического оборудования.
Поскольку это не всегда реально сделать, можно упростить технологию ремонта, применив специальный порядок шлифования вала:
1.Предварительное шлифование коренных шеек но с припуском не менее 0,1 мм для окончательной обработки.
2.Шлифование шатунных шеек.
3.Выдержка в течение нескольких часов, контроль деформации вала (на призмах по индикатору)
Таблица 3.3.2 — Ремонтные размеры вкладышей и шеек коленчатого вала КамАЗ-740
Шатунный подшипник | Коренной подшипник | |||||
Диаметр мм | Маркировка вкладыша | Диаметр мм | Маркировка вкладыша | |||
Шейки коленчатого вала | Постели шатуна | Шейки коленчатого вала | Постели блока | |||
79,95 |
85,0 |
740.1004058 Р1 79,95 | 94,95 | 100,0 | 740.1005170Р1 94,95 | |
79,75 | 85,0 | 740.1004058 Р2 79,75 | 94,75 | 100,0 | 740.1005170Р2 94,75 | |
79,50 | 85,0 | 740.1004058 Р3 79,50 | 94,50 | 100,0 | 740.1005170Р3 94,50 | |
Проверка шатунных шеек и шатунных подшипников
Шатунная шейка
![]() |
Рис. 2.145. Измерение овальности и конусности шатунной шейки микрометром |
Проверьте шатунные шейки на наличие признаков неравномерного износа или повреждений. Измерьте овальность и конусность шатунной шейки микрометром. Если шатунная шейка имеет повреждения или ее овальность или конусность превышают предельные значения, замените коленчатый вал или прошлифуйте шатунную шейку с уменьшением ее диаметра до ближайшего ремонтного размера и используйте вкладыши уменьшенного размера.
Предельные значения по овальности и конусности 0,01 мм.
Шатунный подшипник и шатунная шейка

Шатунный болт
![]() |
Рис. 2.146. Схема проверки шатунного болта |
Деформация шатунного болта (болт с затяжкой в зоне пластической деформации).
Измерьте диаметр резьбы шатунного 1 болта 2 в точках «A» и «B» микрометром 3. Вычислите разность диаметров («A» – «B»). Если разность превышает предельное значение, замените шатун.
Схема измерения шатунного болта «a»: 32 мм, «b»: 40 мм.
Предельное значение разности диаметров шатунного болта («A» – «B»): 0,1 мм.
Общие сведения о шатунных подшипниках (вкладышах)
Для ремонта поставляются шатунные подшипники номинального размера и подшипники увеличенной (под шейки коленчатого вала уменьшенного диаметра) на 0,25 мм толщины, подшипники номинального размера разбиты на 5 видов, отличающихся по допуску.
![]() |
Рис. 2.147. Шатунный вкладыш: 1 – красная краска |
Для идентификации подшипника увеличенной толщины, используется маркировка красного цвета, которая нанесена, как показано на рисунке 2.147, толщина подшипника увеличенной толщины составляет 1,605–1,615 мм в центральной части.
Осмотр шатунного подшипника
Проверьте вкладыши подшипника на наличие признаков оплавления, точечной коррозии, прожога или расслаивания, также осмотрите отпечаток пятна контакта. Дефектные вкладыши подшипников должны быть заменены.
Зазор между вкладышами и шатунными шейками коленчатого вала
Перед проверкой зазора в подшипнике очистите подшипники и шатунные шейки.
Установить вкладыши в шатун и крышку шатуна.
Положите отрезок калиброванной пластмассовой проволоки 1 на поверхность шатунной шейки (параллельно коленчатому валу) так, чтобы он не закрывал масляный канал.
![]() |
Рис. 2.148. Укладка отрезка калибровочной проволоки |
Установите крышку шатуна 1 на шатун.
![]() |
Рис. 2.149. Установка крышки шатуна |
При установке крышки следите за тем, чтобы метка в виде стрелки 2 на крышке была обращена в сторону шкива коленчатого вала, как показано на рисунке 2.149. Смажьте моторным маслом шатунные болты, постепенно затяните глухие гайки 3 следующим образом.
а. Затяните все гайки моментом 15 Н·м.
b. Повторно доверните их на 45°
c. Повторите операцию b) еще раз.
Момент затяжки
Глухая гайка шатунного подшипника (a): затяните моментом 15 Н·м, доверните на 45° и 45°
Снимите крышку и определите величину зазора по сплющиванию калиброванной пластмассовой проволоки 2 в самом широком месте, используя шкалу 1 на упаковке калиброванной пластмассовой проволоки.
Если зазор превышает предельное значение, используйте новый подшипник номинального размера. После подбора нового подшипника снова проверьте зазор.
Зазор в шатунном подшипнике
Номинальное значение: 0,029–0,047 мм.
Предельное значение: 0,065 мм.
Если зазор не может быть приведен в норму установкой нового подшипника номинального размера, прошлифуйте шатунную шейку до ближайшего ремонтного размера и используйте подшипник увеличенной на 0,25 мм толщины.
ПРИМЕЧАНИЕ После проверки зазора в шатунном подшипнике проверьте деформацию шатунных болтов. |
Подбор шатунных подшипников
![]() |
Рис. 2.151. Маркировка на шатуне и его крышке: A – № внутреннего диаметра нижней головки шатуна; B – метка указания веса |
Проверьте № на шатуне и его крышке, как показано на рисунке 2.151.
ПРИМЕЧАНИЕ Если подшипник находится в неудовлетворительном состоянии или зазор в подшипнике – отличается от нормы, подберите и установите новый подшипник номинального размера следующим образом. При замене по любой причине коленчатого вала или шатуна с подшипником, подберите новые подшипники номинального размера по номерам, выбитым на шатуне и его крышке и/или буквам, выбитым на щеке коленчатого вала возле 3-го цилиндра. |
Три № («1», «2» и «3») соответствуют следующим внутренним диаметрам нижней головки шатуна.
Например, № «1» указывает, что внутренний диаметр нижней головки шатуна составляет 45,000–45,006 мм.
Внутренний диаметр нижней головки шатуна

Затем проверьте диаметр шатунной шейки коленчатого вала. На щеке коленчатого вала №3 выбито четыре буквы, как показано на рисунке. Три буквы («A», «B» и «C») соответствуют следующим диаметрам шатунных шеек коленчатого вала. Например, буква «A» указывает, что соответствующий диаметр шатунной шейки коленчатого вала составляет 41,994–42,000 мм
Наружный диаметр шатунной шейки коленчатого вала

![]() |
Рис. 2.152. Маркировка наружного диаметра шатунных шеек коленчатого вала: A – диаметр шатунной шейки коленчатого вала цилиндра №1; B – диаметр шатунной шейки коленчатого вала цилиндра №2; C – диаметр шатунной шейки коленчатого вала цилиндра №3; D – диаметр шатунной шейки коленчатого вала цилиндра №4 |
![]() |
Рис. 2.153. Цветовая маркировка вкладышей шатунных подшипников: 1 – цветовая маркировка |
Существует пять видов подшипников номинального размера, отличающиеся по толщине. Для различия они имеют идентификационные метки следующих цветов в местах, показанных на рисунке 2.153.
Каждый цвет соответствует определенной толщине центральной части подшипника.
Толщины шатунных подшипников номинального размера

Таблица подбора шатунных подшипников номинального размера

![]() |
Рис. 2.150. Измерение сплющенного отрезка калибровочной проволоки |
Используя шкалу 1 на упаковке с калиброванной пластмассовой проволокой 2, проверьте зазор в подшипнике для подобранного подшипника номинального размера (рис. 2.150). Если величина зазора все еще превышает предельное значение, установите подшипник увеличенной толщины и снова проверьте зазор.
Нормальные, допустимые, предельные отклонения размеров форм и взаимного расположения типовых поверхностей СЧ кривошипно-шатунного и уравновешивающего механизмов
|
Проверка состояния и подбор вкладышей коренных и шатунных подшипников коленчатого вала
Проверка состояния и подбор вкладышей коренных и шатунных подшипников коленчатого валаПроверка состояния и подбор вкладышей коренных и шатунных подшипников коленчатого вала
Проверка состояния![]() |
Несмотря на то, что подшипники коленчатого вала в процессе капитального ремонта двигателя подлежат замене в обязательном порядке, старые вкладыши следует сохранить с целью внимательного изучения их состояния, результаты которого могут дать много полезной информации об общем состоянии двигателя. На иллюстрации приведены примеры типичных дефектов вкладышей подшипников. |
Для осмотра извлеките вкладыши подшипников из своих постелей в блоке двигателя/нижних головках шатунов и коренных/шатунных крышках и разложите их в порядке установки на чистой рабочей поверхности. Организованность размещения вкладышей позволит привязать характер выявленных дефектов к состоянию соответствующих шеек вала.
Грязь и посторонние частицы попадают в двигатель различными путями. Они могут быть оставлены внутри блока в процессе сборки агрегата, либо проникнуть через фильтры или систему вентиляции картера. Все частицы, попадающие в двигательное масло, в конечном итоге, рано или поздно, оказываются в подшипниках. Часто в мягкий материал вкладышей внедряются металлические опилки, образующиеся в процессе нормального срабатывания внутренних компонентов двигателя. Велика вероятность присутствия в подшипниках следов абразива, в особенности, когда не было уделено должное внимание чистке блока после завершения восстановительного ремонта двигателя. Вне зависимости от способа, которым посторонние частицы попадают в двигатель, в результате они с высокой степенью вероятности оказываются внедренными в мягкую поверхность вкладышей подшипников коленчатого вала и легко выявляются при визуальном осмотре последних. Крупные частицы обычно не задерживаются во вкладышах, но оставляют на их поверхности и поверхности шеек вала заметные следы в виде царапин, каверн и задиров. Наилучшей гарантией от такого рода неприятностей является ответственное отношение к чистке компонентов после завершения капитального ремонта двигателя и тщательности соблюдения чистоты при сборке. Частая регулярная смена двигательного масла также позволяет существенно продлить срок службы подшипников.
Масляное голодание может являться следствием нескольких различных, но часто взаимосвязанных явлений. Так, перегрев двигателя ведет к разжижению моторного масла и вытеснению его из рабочих зазоров подшипников. Недостаток смазки подшипников может объясняться чрезмерной величиной рабочих зазоров, а также обычными утечками (внутренними или наружными). Часто встречающейся причиной вытеснения масла из зазоров подшипников является постоянное превышение оборотов двигателя. Нарушение проходимости маслотоков (обычно связанное с неправильным совмещением отверстий при установке компонентов) также ведет к сокращению подачи смазки к подшипникам. Типичным результатом масляного голодания является полное или локальное вытирание/выщербливание поверхностного слоя вкладышей с металлической подложки. При этом рабочая температура может подниматься до такого уровня, что подложка в результате перегрева приобретает голубоватый оттенок.
Существенное влияние на срок службы подшипников оказывает также свойственная владельцу автомобиля манера вождения. Движение с малой скоростью на повышенной передаче приводит к значительным перегрузкам подшипников, сопровождающимся вытеснением масляной пленки из их рабочих зазоров. Такого рода перегрузки приводят к повышению пластичности вкладышей и возникновению трещин в поверхностном слое (усталостная деформация). При этом поверхностный материал начинает крошиться и отделяться от стальной подложки. Эксплуатация автомобиля в городском цикле (частые поездки на короткие расстояния) ведет к развитию коррозии подшипников вследствие того, что недостаточный разогрев двигателя влечет за собой выпадение конденсата и выделение химически агрессивных газов. Данные продукты скапливаются в двигательном масле, формируя шлаки и кислоты. При попадании такого масла в подшипники агрессивные вещества способствуют развитию коррозии вкладышей.
Неправильная установка вкладышей в процессе сборки двигателя также может явиться причиной быстрого их разрушения. Слишком тугая посадка не обеспечивает требуемую величину рабочего зазора подшипников, что приводит к их масляному голоданию. Результатом попадания под вкладыши (в процессе их установки) посторонних частиц является образование возвышений, поверхностный слой с которых быстро вытирается.
Подбор вкладышей
В случае износа или повреждения вкладышей коренных подшипников, а также, когда не удается добиться правильной величины рабочего зазора (см. Раздел Установка коленчатого вала и проверка рабочих зазоров коренных подшипников или Установка шатунно-поршневых сборок и проверка величины рабочих зазоров в шатунных подшипниках коленчатого вала), ситуация может быть исправлена описанным ниже способом, путем подбора и установки новых вкладышей. Если коленчатый вал подвергался проточке, он должен быть укомплектован вкладышами соответствующих ремонтных (с принижением) размеров (в этом случае приведенная ниже процедура производиться не должна). Обычно подбор вкладышей осуществляют специалисты, производившие проточку шеек вала. Вне зависимости от методики определения требуемого размера вкладышей рабочие зазоры подшипников должны быть затем проверены с применением измерительного набора Plastigage (см. ниже).
![]() |
Если не удается скорректировать должным образом величину рабочих зазоров путем подбора вкладышей, вал следует заменить. |
Коренные подшипники
1. При необходимости подбора новых вкладышей СТАНДАРТНОГО размера выбирайте тот, который имеет ту же цветовую маркировку, что и старый.
![]() |
2. Если цветовая маркировка старого вкладыша утрачена, отыщите маркировку, выбитую на блоке в районе расположения крышки соответствующего подшипника. |
![]() |
|
![]() |
4. При подборе новых вкладышей воспользуйтесь соответствующей идентификационной картой цветовой маркировки подшипников. |
Шатунные подшипники
1. При подборе новых вкладышей СТАНДАРТНОГО размера ориентируйтесь на цветовую маркировку снимаемых с автомобиля компонентов.
2. В случае утраты цветового кода на старых вкладышах, отыщите маркировку на нижних головках шатунов. Метка в виде цифры характеризует размерный класс шатунного подшипника (не следует путать ее с номером цилиндра).
3. Проверьте также литерные метки собственно на валу, определяющие размер соответствующих шатунных шеек (см. сопроводительную иллюстрацию).
Идентификационная карта выбора вкладышей коренных подшипников коленчатого вала для 4-цилиндровых двигателей — используйте маркировку, нанесенную на блок двигателя, и сборку коленчатого вала, например: маркировка С3 означает необходимость установки вкладышей желтого и зеленого цветов (где они должны быть разного цвета), причем любой из них может быть установлен как в крышку подшипника, так в его постель в блоке
![]() |
|
Идентификационная карта выбора вкладышей коренных подшипников коленчатого вала для двигателей V6
![]() |
|
![]() |
На 4-цилиндровых двигателях литерно-цифровая маркировка класса подшипниковых шеек нанесена на щеке первого кривошипа или выбита по соседству с каждой шейкой в отдельности. |
Идентификационная карта выбора вкладышей шатунных подшипников коленчатого вала для 4-цилиндровых двигателей — используйте маркировку, нанесенную на щеки кривошипов и соответствующие шатуны, например: маркировка D4 подразумевает необходимость установки вкладышей синего цвета
![]() |
|
Идентификационная карта выбора вкладышей шатунных подшипников коленчатого вала для двигателей V6- используйте маркировку, нанесенную на щеки кривошипов и соответствующие шатуны, например: маркировка D4 подразумевает необходимость установки вкладышей коричневого цвета (обратите внимание, что в некоторых случаях требуется установка комбинации вкладышей двух различных цветов)
![]() |
|
Все подшипники
Помните, что окончательным параметром, определяющим правильность подбора вкладышей, является результат измерения рабочих зазоров в подшипниках. С любыми вопросами смело обращайтесь к представителям фирменных сервис-центров компании Honda.
устройство и размеры, ремонт, замена
Коленвал КамАЗ 740 изготавливается из стали высокого качества, оснащается пятью коренными шейками и четырьмя шатунными аналогами. Эти детали закалены путем воздействия высокой температуры и давления. Между собой элементы соединены специальными щеками и сопряженными гантелями.
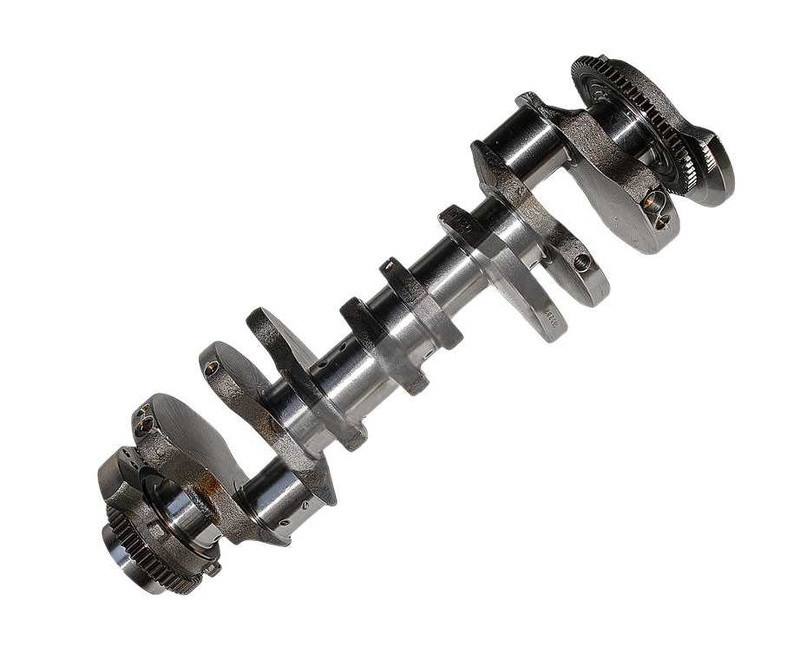
Особенности
Подвод масла осуществляется через специальные отверстия, предусмотренные в коренных шейках. Чтобы уравновесить инерционные воздействия и снизить вибрацию, установили шесть противовесов, изготовленных методом штамповки, как и щеки. Также предусмотрено два добавочных противовеса, которые напрессованы на валу. В расточенном гнезде хвостовика находится запрессованный шариковый подшипник коленвала КамАЗ 740. Угловое размещение деталей относительно коленчатого вала регулируется шпонками.
Равномерное чередование рабочих моментов коленвала КамАЗ 740 обеспечивается за счет расположения шатунных шеек под прямым углом. К каждому элементу подсоединена пара шатунов: для правого и левого цилиндрового ряда.
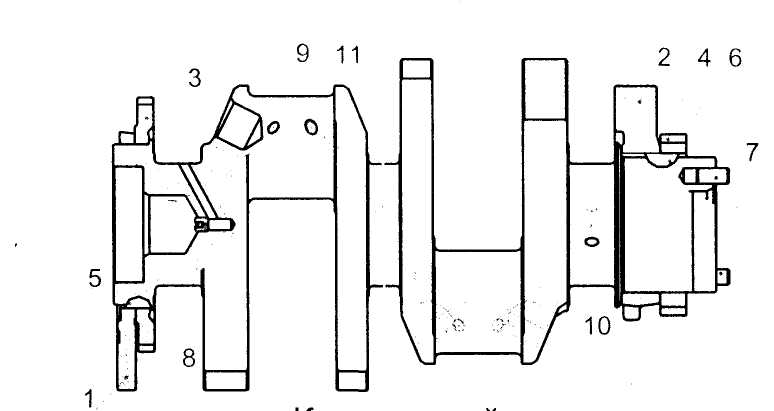
- Противовес передний.
- Задний аналог.
- Приводная шестеренка.
- Зубчатый элемент привода ГРМ.
- Шпонка.
- Шпонка.
- Штифт.
- Жиклер.
- Разгрузочные гнезда.
- Гнезда для подвода масла.
- Отверстия для маслопровода к шатунным шейкам.
Устройство
В полости фронтального носовика узла вкручен жиклер. Через его калибровочное гнездо поступает смазка для шлицевого вала понижения мощности на приводную часть гидравлической муфты. От перемещений по осям коленвал КамАЗ 740 защищен парой верхних полуколец и двумя нижними аналогами. Они монтируются таким образом, чтобы канавки прилегали к торцам вала.
Спереди и сзади на носках блока имеется шестерня привода маслонасоса и ведущий зубчатый элемент распредвала. На заднем торце детали предусмотрено восемь соединений с резьбой для фиксации гасителя вращательных моментов. Уплотнением коленчатого вала служит резиновая манжета, которая оснащается пыльником, располагается в картере маховика. Она изготовлена из фторкаучукового состава непосредственно в пресс-форме.
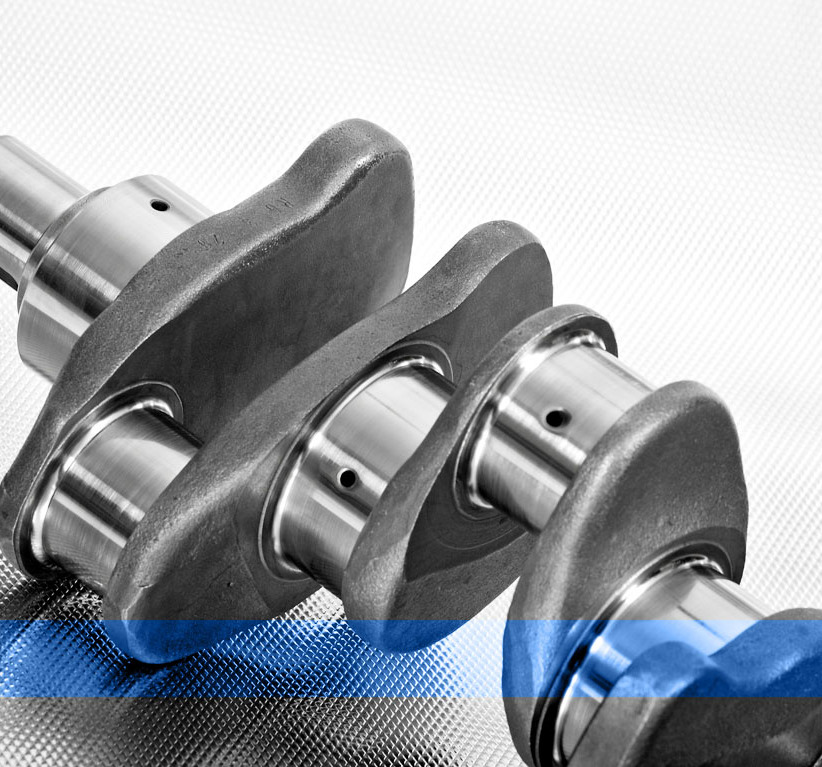
Маховик и шейки
По диаметру коренные и шатунные шейки коленвала КамАЗ 740 составляют 95 и 80 миллиметров соответственно. Предусмотрено 8 типов восстановительных вкладышей, которые применяются для ремонта без проведения шлифовки. Коренные и шатунные подшипники сделаны из стальной ленты со свинцово-бронзовым напылением и оловянным покрытием. Вкладыши вверху и внизу элемента не являются взаимозаменяемыми. От поперечного и продольного смещения они зафиксированы уступами, которые размещаются в пазах крышек подшипников и постелях шатуна. Указанные части имеют соответствующую маркировку (74-05.100-40-58 и 74-05.100-57-51). Заслонки и крышки изготовлены из чугуна повышенной прочности. Крепятся они при помощи болтов, которые фиксируются по регламентированной схеме. Маховик фиксируется на восемь болтовых шпилек, сделанных из легированной стали, а также штифтами с втулкой. Чтобы избежать повреждения узла, под болтовые головки помещаются шайбы, а на цилиндрической поверхности маховика находится зубчатый венчик.
Гаситель вращательных моментов
Коленвал двигателя КамАЗ 740″ оборудуется гасителем вращательных колебаний, который фиксируется восемью болтами на фронтальном носке блока. Деталь включает в себя корпус, который закрыт крышкой. Он с запасом хода монтируется в маховике. Герметичность соединений достигается при помощи сварочных швов по стыкам основы и крышки.
Между остовом и маховиком работает силиконовый состав повышенной вязкости. Жидкость заправляется дозировано перед фиксацией крышки. По центрам гаситель регулируется посредством шайбы, приваренной к основе. Нивелирование вращательных моментов происходит при помощи торможения остова гасителя. Данная энергия выделяется как тепловой поток. Стоит отметить, что при ремонте узла воспрещается нарушать целостность корпуса и крышки. Блок с деформациями для дальнейшего использования становится непригодным.
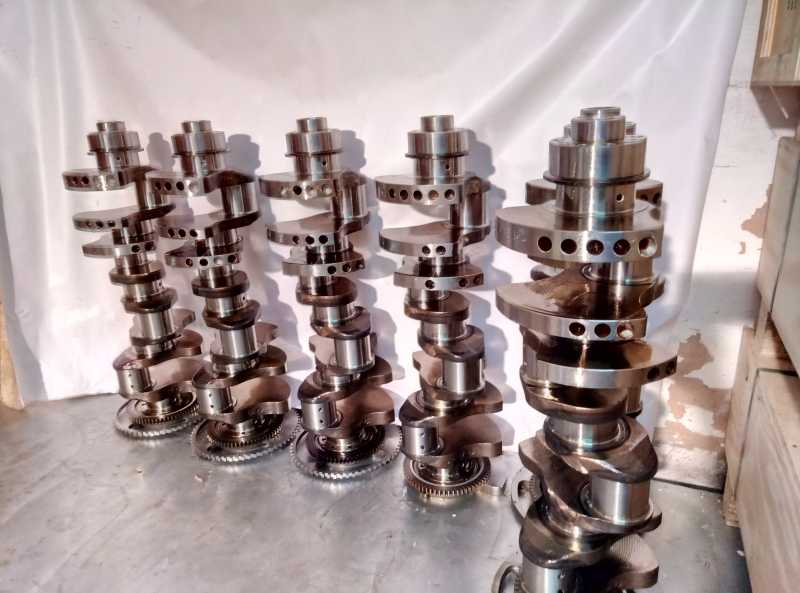
Шатунно-поршневая группа
Шатун коленвала КамАЗ 740 10 сделан из стали методом ковки. Он оснащен стержнем с двутавром, головка вверху — неразъемного типа, снизу — сделана с прямым разъемом. Окончательная обработка шатуна производится в сборе с крышкой, которая не является взаимозаменяемой для аналогов. В верхней головке детали имеется втулка из сплава бронзы и стали, которая установлена путем прессовки. В нижней части смонтированы сменные вкладки.
Нижняя крышка фиксируется болтами с гайками, которые запрессованы в стержень. На элементы наносятся метки сопряженности в виде порядковых номеров из трех знаков. Также на крышке выбивается номерное клеймо цилиндра. Поршень отливается из алюминиевого состава, имеет вставку из чугуна для верхнего кольца компрессии. Также головка поршня оснащается камерой сгорания с центральным вытеснителем. Элемент смещен по оси в направлении от клапанных выточек на пять миллиметров. Боковая часть имеет бочкообразную конфигурацию с уменьшением размера в районе отверстий под палец поршня.
Компрессионные и маслосъемные элементы
Поршень комплектуется сальником коленвала КамАЗ 740, а также парой компрессионных колец и одним маслосъемным аналогом. Дистанция от днища до нижней торцевой части верхней канавки 17 мм. Поршневая часть моторов 740/11, 740/13 и 740/14 между собой отличается формой гнезд под кольца, поэтому не является взаимозаменяемой.
Компрессионные элементы сделаны из усиленного, а маслосъемное кольцо — из серого чугуна. На «движке» 740/11 конфигурация поперечного сечения фиксаторов — односторонняя трапеция. При установке верхний наклонный торец размещается со стороны поршневого дна. Рабочая бочкообразная часть кольца покрыта молибденом. На поверхность второго компрессионного и маслосъемного кольца нанесено хромовое напыление.
При установке середина расширителя располагается в специальном замке. Маслосъемное кольцо изготовлено коробчатой конфигурации, на моторе 740/11 имеет высоту 5 миллиметров, а на 740/13 и 740/14 — 4 мм.

Ремонтные размеры коленвала КамАЗ 740
Ниже в таблицах приведены габариты, при которых допускается восстановление частей узла:
Разновидность | Размер шейки основной (мм) | Отверстие в узле цилиндров (мм) |
РО-1 | 94,7 | 100 |
РО-2 | 94,5 | 100 |
Р10 | 95,0 | 100,5 |
Р11 | 94,75 | 100,5 |
Р12 | 94,5 | 100,5 |
Р13 | 94,25 | 100,5 |
РО3 | 94,25 | 100 |
Номинальные размеры коленвала КамАЗ 740 для ремонта и замены вкладок:
Обозначение | Диаметральный размер шейки шатуна в диаметре (мм) | Отверстие в кривошипе шатуна по диаметру (мм) |
РО1 | 79,75 | 85,0 |
РО2 | 79,5 | 85,0 |
РО3 | 79,25 | 85,0 |
Р10 | 80,0 | 85,5 |
Р11 | 79,75 | 85,5 |
Р12 | 79,5 | 85,5 |
Р13 | 79,25 | 85,0 |
Ремонтный комплект
В восстановительный набор коленвала КамАЗ 740 бу входят следующие элементы:
- поршень с кольцами;
- пальцевые и стопорные элементы;
- цилиндровая гильза;
- уплотнительные детали.
Охлаждающие форсунки узла монтируются в картере блока цилиндров, отвечают за своевременную подачу масла из главной магистрали при давлении 0,8-1,2 кг/кв.см. На такое значение обычно откорректирован клапан. Масло подается во внутреннюю часть поршней. При сборке двигателя 740-го КамАЗа предусматривается контроль трубки форсунки по отношению к гильзам поршня и цилиндра, при этом прямой контакт с первым элементом не допускается.
Шатун и поршень соединяются при помощи пальца плавающего вида. По осям перемещение детали ограничивают стопорные кольца, а сам элемент изготавливается из хром-никелевого сплава, диаметр гнезда — 22 мм. Эксплуатация аналога размером 25 мм не допускается, поскольку это нарушает балансировку силового агрегата.
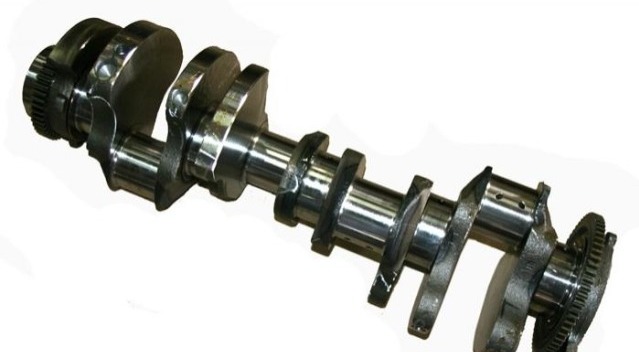
Восстановление коленвала на примере
Чтобы понять особенности ремонта рассматриваемого узла, изучим один из примеров его починки. Коленчатый вал был взят со списанного грузовика, возившего комбикорма. После доставки детали ее вскрыли, сняли поддон, открутили шатун, вкладыши, коренную шейку. Оказалось, что в качестве уплотнителей под бугелем были установлены прокладки из жестяной банки. Вкладыши полностью пожелтели и не представляли собой годные элементы, поскольку слишком заметной была выработка рабочих гнезд.
Решили снять вал и отправить его на шлифовку, при этом на вкладышах наблюдалась деформация в виде царапин. При этом шатунные шейки и вал оказались в отличном состоянии. Коренные аналоги вывели под второй ремонт. Кстати, чистка и мытье коленчатого вала можно эффективно осуществить следующим способом:
- подсоединяют пульверизатор к компрессору;
- наливают в емкость дизельное топливо;
- под коленвал укладывают чистый картон;
- промывают узел, пока на подстилке перестанут показываться грязные пятна и стружка;
- солярку разогревают до горячего состояния, во второй распылитель заливают бензин.
Опыт показал, что такая чистка коленчатого вала очень эффективна и позволяет достичь уровня заводской подачи.
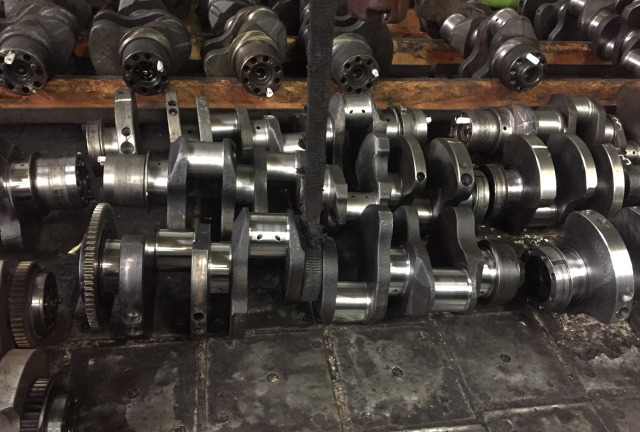
В завершение
Коленчатые валы КамАЗ 740 проходят классическую закалку путем воздействия токами высокой частоты. Глубина защищенного и обработанного слоя составляет порядка трех миллиметров. Это позволяет получить высокий показатель твердости на всех стадиях восстановления узла. Указанный параметр составляет до 62-х HRC. В последнее время выпускаются детали, обработанные путем азотирования. То есть, коленвал упрочняют термохимическим способом, что дает возможность увеличить твердость, но уменьшает глубину закаленной части. Например, после шлифовки указанным способом появляется проблема в необходимости повторной обработки, что не всегда актуально в сложившихся условиях.
Оставить ответ