О толщине нанесения автомобильных красок и лаков
Вряд ли кто будет спорить с тем фактом, что чем толще слой лака на автомобиле, тем выше визуальные характеристики лакокрасочного покрытия. Достаточно взглянуть на престижные авто представительского класса, дорогие лимузины или концепт кары… Многие наслышаны о тех неимоверных количествах эмалей и лаков, затрачиваемых при окраске таких автомобилей их производителями или тюнинг-компаниями.
Слой прозрачного лака на кузовах эксклюзивных и дорогих авто может достигать толщины в 300 (!) и более микрон (забегая наперед отметим, что на их серийных собратьях этот показатель обычно не превышает и 60-ти).
В силу этого обстоятельства и некоторых других факторов (в частности, желания произвести как можно более впечатляющий эффект на потенциального покупателя автомобиля, рассчитывая на адекватную толщину его кошелька) в рядах отечественных маляров сформировалось некое заблуждение, упрощенно которое можно описать так: «дополнительный слой лака лишним не бывает!»
И коль недостатка в лаке маляр не испытывает, он начинает лить его не жалея… Мол, что здесь нетехнологичного? Тем более, что остался разбавленный с отвердителем лак, куда его прикажете девать? Да и сорность, порой, большая — запас под полировку нужен.
Конечно, ни о каких трехста микронах здесь речи не идет. Все мы понимаем, что достижение такой толщины возможно лишь при многоразовом чередовании нанесения лака, его сушки, поверхностной шлифовки и нанесения следующих слоев лака. Интересно было бы посмотреть на попытку нанесения покрытия такой толщины за один раз!
Рекомендованная толщина слоя
Для достижения покрытием необходимой механической прочности, его гарантированных декоративных и антикоррозионных свойств, практически все производители ЛКМ дают рекомендации по нанесению прозрачного лака или акриловой эмали толщиной в пределах 50-70 микрометров.
При пневматическом распылении такая толщина достигается за полтора (для HS-материалов) или два (для MS) слоя, поскольку попытка нанести такую толщину за один проход грозит возникновением двух основных дефектов лакокрасочного покрытия: подтеков или вскипания и помутнения лака (хотя из всякого правила есть исключения — однослойные UHS/VHS-материалы).
То есть, в среднем, один рекомендованный слой лака должен равняться примерно 30 микрометрам. Тогда два слоя — 60 мкм, — как раз в пределах нормы. Три слоя — это уже 90 мкм. О чем это говорит?
А о том, что даже если горизонтальные поверхности и смогут пережить такое превышение вполне сносно, но и на них значительно возрастает вероятность вскипания лака. А вскипание, как известно, зараза хитрая — оно сопровождается еще и ухудшением блеска. Сколько потом ни полируй лак, он все равно через некоторое время будет матоветь. А что вы хотели? Молекулярные цепочки сшились некорректно, твердость пропала, а вместе с ней ушел и глянец. Такое явление особенно характерно для дешевых лаков с низким сухим остатком и большим количеством растворителя в составе.
Кроме того, возможны, пусть и незначительные, но не особо радующие глаз наплывы (например по периметру капота).
Во-вторых, на вертикальных элементах избыточная толщина слоя неминуемо приведет к его смещению по всей плоскости, значительно возрастает риск образования подтеков. Но даже если этого и не произойдет, фактура покрытия (шагрень) после высыхании будет хуже, чем при рекомендованном слое.
В-третьих, не надо забывать про межслойную выдержку. Если слоев больше, мы потратим лишнее время на паузу между ними, общее время ремонта увеличивается. А это уже минус.
Но еще хуже, если поторопимся, нанеся дополнительный слой без достаточной выдержки.
Рекомендованные промежутки между слоями ведь зачем нужны? Чтобы дать возможность испариться из слоя высоколетучим растворителям. Попытка нанести последующий слой с недостаточной паузой или без нее приводит к образованию на поверхности большого количества мельчайших пор (то самое «кипение»).
Это — следствие интенсивного выхода большого количества быстрых растворителей, оставшихся в нижнем слое. Покрытие при этом теряет блеск и мутнеет, могут появиться подтеки. Ухудшаются и адгезионные свойства покрытия.
И, наконец, мы затратим значительно больше времени на сушку покрытия такой толщины, дольше высыхая, слой лака впитает больше мусора — отсюда лишние проблемы при полировке. Растворителя в толстом слое останется больше, а твердость его, соответственно, будет ниже.
Да и все равно до 300 микрон еще ох как далеко! Ну, и стоило ли стараться?
Мораль
Только оптимальная толщина слоя лака или эмали обеспечивает хорошую растекаемость, стойкий блеск и высокую прочность покрытия и гарантирует отсутствие дефекта «закипания».
При стандартной толщине пленки лак всегда высыхает быстро и полностью, после чего отлично полируется. А при нанесении слишком толстым слоем любой, даже самый дорогой и технологически «продвинутый» лак будет сохнуть медленнее, хуже полироваться и блестеть, чем самый обычный, но грамотно используемый материал. То же самое можно сказать и о нанесении эмалей либо грунтов.
Ну а если вы решительно настроены наращивать пленку лака, делать это нужно особым образом. Не нужно наносить слишком толстые слои — лучше разделить нанесение на несколько тонких, при этом выдержку им давать не меньше, чем нормального слоя. В таком случае у нас получится избежать «кипения».

Технология покраски автомобиля «металликом»
В силу тех или иных причин количество автомобилей, окрашенных «металликами» растет, но вот страдают в авариях они почему-то точно так же, как и остальные. А ремонтная окраска таких машин предъявляет серьезные требования к квалификации маляра. Главная причина заключается в том, что как ни крути, а металлические частицы, содержащиеся в этих красках, — это все-таки нерастворимые инородные тела, которые в слое краски могут вести себя абсолютно непредсказуемо и своенравно.
Поэтому для успешной работы с металлизированными эмалями маляр должен не только упражняться в нанесении краски, но и изучать теорию — разбираться в важнейших свойствах «металликов» и принципах «поведения» этих красок.
Сегодня вы узнаете
Прежде чем…
Учитывая то, что каждый человек обладает определенной степенью образного представления того или иного описываемого процесса, а также для того, чтобы придать нашему «техническому» повествованию немного художественного стиля, мы уточним что, как и чем мы планируем красить.
Допустим, у нас пострадал в аварии, а затем был восстановлен и подготовлен к покраске красивый, современный, новый, дорогой, элегантный (думается, достаточно прилагательных, чтобы немного вас напугать) автомобиль, окрашенный светлым серебристым металликом.
Не углубляясь в изначальные нюансы повреждений, ремонта или замены той или иной детали, остановимся на том, что восстановленные кузовные элементы загрунтованы по всей плоскости, тщательно зашлифованы (под металлик это делается абразивным материалом P400-Р500 «по-сухому» или P800-Р1000 «по-мокрому») и предназначены для полной перекраски. Это важно, так как в этом случае серьезно стоит вопрос о точности подбора оттенка эмали, или о необходимости выполнения плавного перехода на соседние элементы.
Кстати, для нашего примера неспроста был выбран именно серебристый металлик. Светлые и серебристые цвета содержат очень много алюминиевого зерна и крайне непредсказуемо отражают световые потоки, поэтому по сравнению с темными «металликами», они особенно сложны в ремонтной окраске.
Результат здесь зависит от массы факторов: при каком давлении распылять, соблюдены ли пропорции смешивания с разбавителем, какой толщины слой наносить, какую паузу между слоями выдерживать и т. д.
Серьезные ошибки, допущенные на этапе приготовления или нанесения краски, могут свести все старания маляра на нет, и потребовать после высыхания повторной перешлифовки и перекраски.
Например, если попытаться «сэкономить» и использовать при покраске разбавитель другой фирмы, цвет металлика может существенно уйти!
Дело в том, что фирменные разбавители для металликов специально подбираются так, чтобы за время их испарения алюминиевые частички «утонули» на нужную глубину и правильно распределились в слое краски (от этого зависит ее оттенок). Замена же разбавителя, на, например, более быстроиспаряющийся, может привести к осветлению покрытия и возникновению таких дефектов, как полосы и «облака».
Помочь избежать подобных ошибок позволит внимательное отношение к рекомендациям производителя по применению материалов: пропорции их приготовления, выбор разбавителей, рабочая вязкость, режимы нанесения и т.д.
Для разбавления базы следует использовать только оригинальный разбавитель, а его тип должен соответствовать температуре, при которой будет вестись покраска.
Но будет обидно, если работу придется переделывать не столько из-за причин, зависящих от технологии нанесения краски, сколько из-за собственной неаккуратности. Это могут быть жировые кратеры (плохо обезжирили), грубые вкрапления пыли, особенно под слоем базовой краски (не обдули), пузырьки и другие дефекты.
Чтобы свести к минимуму возникновение подобных неприятностей, перед окраской не забудьте тщательно обезжирить поверхность, а затем произвести пылеудаление с помощью обдува сжатым воздухом и специальной липкой салфетки.
Вернемся к нашему автомобилю. Вот он, родимый: оклеен, обезжирен и готов к покраске.
Можно заливать краску в бачок окрасочного пистолета и… Кстати, о пистолете.
Инструмент серебряника
Современные базовые эмали требуют применения окрасочных пистолетов с низким давлением воздуха на выходе. Дешевые конвенциональные распылители, в широком ассортименте представленные на рынке, здесь плохие помощники. Их высокое давление иногда позволяет получить широкий факел, но при нанесении «выбивает» из материала большое количество растворителя, и краска укладывается на поверхность фактически без него. На металликах это неминуемо приводит к появлению полос и «облаков», особенно на серебристых цветах. Вот, полюбуйтесь…
Если же использовать вместо конвенциональных пистолетов краскопульты более прогрессивных систем (HVLP или LVLP), риск образования подобных дефектов значительно снизится. Низкое давление на выходе у таких распылителей позволяет донести до поверхности достаточное количество растворителя для того, чтобы зерна металлика легли на поверхность в правильном виде.
Не забудьте перед покраской убедиться, что краскопульт обеспечивает достаточно широкий и равномерный по всей ширине окрасочный факел, а отпечаток факела имеет правильные очертания.
Для нанесения базовых эмалей рекомендуется использовать пистолет с диаметром сопла 1,3-1,4 мм. Давление воздуха должно быть точно выставлено непосредственно на пистолете (как правило 2-2,2 бар) и не колебаться в процессе работы. Воздух должен быть очищен от масла и влаги.
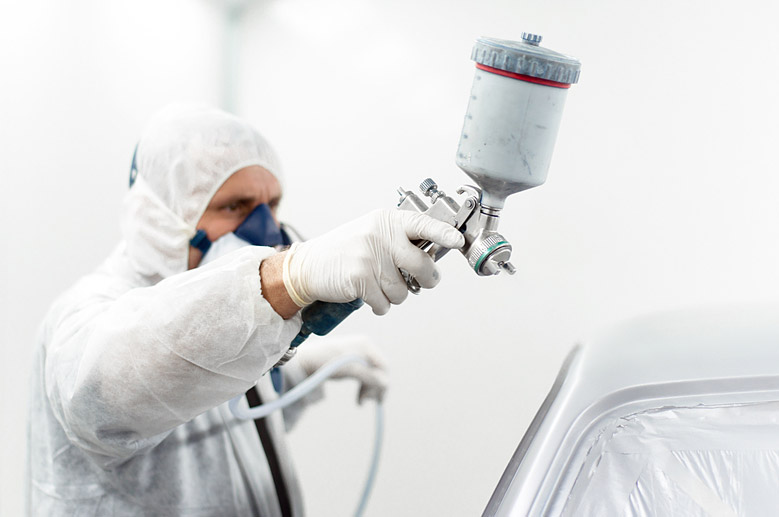
«А «металликом» красить умеешь?». Такой вопрос в начале 90-х годов задавали любому маляру, решившему устроиться на автосервис. Сейчас, когда маляры с легкостью справляются с обычным «металликом», к их квалификации предъявляются уже новые требования: в частности, навыки работы со светлым «металликом»
А не посеребрить ли нам… кузов!
В эмалях с металлическим эффектом важнейшую роль играет отражение света. Как известно, в составе этих красок, помимо цветовых, содержатся еще и эффектные пигменты — алюминиевые частицы. Они выполняют роль крошечных непрозрачных зеркал, отражающих падающий свет, что и придает покрытию эффект характерного сверкающего блеска.
Более того, если посмотреть на деталь, окрашенную металликом с разных сторон, то хорошо видно, что этот блеск не постоянен — его интенсивность то убывает, то прибавляется. В самом деле, любой «металлик», в зависимости от угла наблюдения будет выглядеть по-разному: покрытие ярко светится, искрится в некоторой точке, а затем постепенно темнеет при изменении угла обзора (например, когда машина поворачивает). Эти изменения, от светлого к темному и обратно, называются «флоп-эффектом».
Основная и самая сложная задача, стоящая перед маляром при работе с металликом, заключается в том, чтобы правильно «уложить» частицы алюминия в слое краски. От того, как лягут эти частицы, будут полностью зависеть декоративные свойства полученного покрытия.
Если мы сумеем сориентировать эти частицы как нужно, то есть параллельно подложке и друг другу, покрытие в этом случае будет обладать оптимальными оптическими свойствами. Но если «серебро» ляжет в слое краски хаотично, рассеивая свет в разные стороны, это приведет к искажению цвета, нарушению флоп-эффекта и возникновению характерных для металликов «облаков».
Как мы уже говорили, серебристые цвета в этом плане особенно капризны, поскольку они почти не содержат цветовых пигментов. Их цвет, по сути состоит из одного только алюминиевого зерна, ответственного за флоп-эффект. Работа с такими цветами требует от маляра особенной внимательности и ясного понимания поведения алюминиевых частиц в слое краски.
Факторы, влияющие на металлик. Толщина слоя и другие
На ориентацию алюминиевых частиц влияет масса факторов, но все эти факторы так или иначе связаны со скоростью испарения растворителя и глубиной «залегания» алюминиевого зерна в слое краски.
В первую очередь, для равномерного разложения «серебра», следует избегать как слишком мокрого, так и слишком сухого нанесения базы.
В слишком мокром слое растворителя будет больше, а значит испаряться с окрашенной поверхности он будет дольше (то есть толстый слой будет большее время оставаться жидким). В этом случае алюминиевые частицы имеют тенденцию к тому, чтобы «тонуть» в нижнюю часть слоя и перед высыханием ориентируются вертикально по отношению к подложке. Глубоко утонувшее зерно практически перестает отражать падающий на него свет, что приводит к искажению цвета — он темнеет.
И наоборот. Если эмаль попадает на поверхность в слишком сухом состоянии, растворителя в таком слое, наоборот, будет меньше, испарится он быстрее, и зерно не успеет утонуть на положенную глубину и занять правильное положение в слое краски. Оно останется на поверхности слоя, отражая слишком много света, что приведет к осветлению покрытия и потере насыщенности цвета. Кроме того, база, которая легла на поверхность «ежом» приводит к повышенному расходу лака, его неравномерной усадке и понижению блеска после сушки.
Как в первом, так и во втором случае возможно образование полос и «облаков».
Чем толще слой металлика, тем дольше он будет оставаться жидким, тем глубже в нем успеет утонуть зерно и тем темнее будет общий оттенок покрытия. И наоборот.
В правильно нанесенном слое металлика — слое средней толщины, не сухом, и не жирном — зерна алюминия залегают на положенную, стандартную глубину, ориентируясь параллельно подложке. При этом достигается наилучшее проявление «флоп-эфекта», обеспечивается однородность цвета и хорошая укрывистость эмали.
Все остальные факторы, точно так же как и фактор толщины слоя нужно рассматривать через призму их влияния на скорость испарения растворителя и глубину залегания алюминиевого зерна.
Например:
- При превышении рекомендованного давления распыления из окрасочного факела будет «выбиваться» большее количество растворителя, а значит на окрашенную поверхность его попадет меньше, испарится он быстрее, зерно останется в слое выше, и покрытие приобретет более светлый оттенок.
- Чем ниже вязкость распыляемой краски, тем тоньше получается слой и быстрее его испарение. Соответственно, за более короткое время зерно успеет утонуть на небольшую глубину, и покрытие получится светлее.
- Чем выше температура окружающего воздуха, тем выше скорость испарения растворителя, и тем светлее получится общий оттенок эмали.
- Чем больше расстояние от пистолета до окрашиваемой поверхности, тем большая часть растворителя распыляется, не попав на поверхность. Значит, в слое его останется меньше, он испарится быстрее, и покрытие будет выглядеть светлее.
- Чем быстрее проходы, тем меньше растворителя перенесется на поверхность, и тем светлее будет выглядеть покрытие.
- Чем более быстрый разбавитель используется, тем выше скорость его испарения, а значит зерно в слое останется выше и покрытие будет иметь более светлый оттенок.
И так далее.

Методы влияния на оттенок металлика. Понимание этих взаимосвязей на практике может помочь нивелировать небольшие различия в оттенке и «вытянуть» цвет
На рисунке ниже схематично показано, как влияет глубина залегания алюминиевых частиц на общий оттенок покрытия.
Из схемы видно, что при нормальном расположении зерен наш глаз воспринимает и цвет покрытия, за который отвечают цветовые пигменты, и зерно, равномерно распределенное в слое краски (рис. А).
Если зерно не успело утонуть на положенную глубину и осталось в верхних слоях покрытия, оно закрывает собой цветовые пигменты, и наш глаз улавливает лишь свет, отраженный зерном, из-за чего покрытие воспринимается как более светлое (рис. Б).
Глубоко утонувшее зерно «прячется» за цветовые пигменты и практически не отражает падающего на него света, и наш глаз воспринимает оттенок покрытия как более темный (рис. В).
Следите за руками
При нанесении металлика критично важную роль играет техника распыления. Важно придерживаться правильного положения краскопульта и равномерной скорости движения. Если хоть на секунду приостановить движение и слой краски успеет напылиться толще, чем рядом — полос и «яблок» не миновать.
Держать пистолет нужно строго под прямым углом к окрашиваемой поверхности, иначе, при наклоне, в верхней и нижней частях факела расстояние до поверхности будет разным, а значит в одном месте слой получится толще, в другом — тоньше.
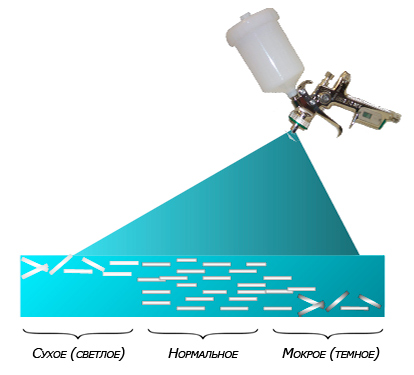
Неравномерность толщины слоя краски приводит к различной ориентации алюминиевых частиц на различных участках слоя. Из-за этого возникает дефект, который обычно называют «облака» или «яблоки»
Количество слоев и межслойная сушка
Итак, для достижения наилучшего результата окраску металликом следует вести равномерными «полумокрыми» слоями: не сухими, но и не слишком мокрыми. Количество слоев?
Зависит от укрывистости базы, но чаще всего используется классическая технология: 2+1.
То есть наносятся два кроющих слоя (их допускается наносить более мокро), после чего напыляется так называемый капельный слой (он же эффектный, дымчатый, выравнивающий и т.д.) — он нужен для коррекции оттенка и устранения «яблочности».
Капельный слой наносится следующим образом. Понижаем входное давление на пистолете до 1-1,5 атм. (при нажатом курке и без изменения подачи, либо с немного увеличенной подачей) и, после того, как последний слой базы поматовел, с чуть большего расстояния (приблизительно 30 см) напыляем полумокрый капельный слой, который, словно «дождик», должен равномерно и аккуратно покрывать поверхность. После нанесения образовавшиеся капельки быстро растянутся и покрытие станет гладким.
Обычно 2-3 слоев базы хватает, но для плохоукрывистых цветов иной раз мало не то что трех, а и пяти слоев. В этом случае поможет колеруемый грунт, о котором нужно позаботится заранее.
И не забывайте о межслойной выдержке. Недостаточная пауза может послужить поводом для облачности и других дефектов, поэтому наносите следующий слой базы только после того, как предыдущий стал матовым. Обычно это 5-10 минут (при 20 °C).
А не пора бы нанести лак?
Итак, мы нанесли базовую эмаль, но, тем не менее, выглядит наш автомобиль пока еще довольно убого. Чтобы довести дело до логического завершения, осталось нанести поверх базы прозрачный лак. После этого покрытие станет не только сказочно красивым, но и стойким к внешним воздействиям (база сама по себе не отличается атмосферостойкостью).
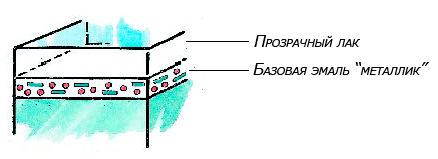
В отличие от однослойных металлизированных красок первого поколения, современные «металлики» представляют собой двухслойную систему: поверх базовой эмали нанесен прозрачный лак
Главный вопрос: через сколько можно наносить лак?
Здесь важно, как говорится, не прохлопать момент, поскольку базовая эмаль сохраняет способность «впитывать» последующие наносимые слои строго определенное время. Если это время упущено, межслойная адгезия между базой и лаком будет нарушена, и в процессе эксплуатации лак с пересушенной базы обязательно будет отслаиваться.
Иногда мастера допускают грубейшую ошибку: вечером наносят базу, а лаком покрывают на утро, аргументируя это тем, что краска за ночь наверняка подсохнет. С металликами такой подход в корне неправильный!
Лучше всего при нормальной температуре покрывать базу лаком уже минут через 15-20. Это идеально. За это время из базы улетучатся растворители, она заматовеет, и будет полностью готова принять на себя лак.
Но если покрыть лаком еще жидкий, не испарившийся базовый слой, это может привести к матовению ЛКП, а также проявлению «облаков» (зерна как бы «слипаются», неравномерно отражая свет). Поэтому при низких температурных режимах окраски время выдержки должно быть увеличено (до полного матовения базы).
Максимальное время, при котором не происходит нарушение межслойной адгезии между базой и лаком обязательно указывается в технической документации к той или иной эмали. У разных производителей это время может быть разным, но практика показывает, что если мы не покроем базу лаком в течении часа, максимум двух, то максимальной адгезии у нас уже не будет.
Поэтому если вы опоздали, базовый слой должен быть заматирован и перекрашен заново.
Подробнее о нанесении лаков читайте здесь.
Перед нанесением прозрачного лака базовый слой необходимо обработать липкой салфеткой для удаления опыла, пыли и ворса.
По завершении работ…
Есть еще один немаловажный аспект в работе маляра, которому обычно не придают серьезного значения. Это мойка пистолета после работы с металликом. Если делать эту операцию спустя рукава, то в пистолете могут оставаться частицы «серебра», которые потом либо засоряют дюзу и портят форму факела, либо вылетают на поверхность при очередной окраске.
Поэтому по завершении работ нужно позаботиться о чистоте инструмента. Окрасочный пистолет тщательно промывается растворителем и продувается сжатым воздухом. Не жалейте на это сил и времени.
Радуясь от всей души блеску окрашенного после ремонта крыла или капота, да еще и металликом, да еще и серебристым, да еще и без «яблок», да еще и… (простите, увлеклись) поневоле ощущаешь радость владения автомобилем. Да, да! Такой он красивый, блестящий, гладкий, свежий, неподражаемый, совершенный, коррозионноустойчивый, на четырех колесах, пятиступенчатая коробка передач… Простите, опять увлеклись…

Несколько лет проработал в области кузовного ремонта. Затем заинтересовался созданием веб-сайтов и запустил проект Artmalyar.ru, на страницах которого делюсь накопленным опытом в кузовном деле.
Также запущен сервис ASK.artmalyar, где вы можете задать вопросы лучшим мастерам кузовного ремонта, и раздел Технической документации, где собраны инструкции к материалам и инструментам для покраски автомобилей.
-
Покраска трехслойным «перламутром» «в переход»
Особенности трехслойных покрытий, подготовка поверхности, нанесение подложки, перламутра и лака.
-
Эффектные ЛКП: «перламутр» и «ксираллик»
Особенности красок с эффектом «перламутр» и «ксираллик», принципы достижения эффектов, структура компонентов.
-
Технология покраски «металликом»
Учимся красить «металликом»: факторы, влияющие на металлик, толщина и количество слоев, время сушки между слоями и перед нанесением лака, техника нанесения.
Загрузить больше
-
Тест: Какой из тебя маляр?
Предлагаем вам проверить свои знания в области подготовки и окраски, ответив на 20 вопросов нашего теста.
-
О чистоте сжатого воздуха для окрасочных работ
Поговорим об источниках и составе загрязнений сжатого воздуха и о требуемом качестве воздуха для окраски.
-
Покраска новых деталей. Метод «мокрый по мокрому»
Учимся красить новые детали с использованием технологии «мокрым по мокрому».
Больше в категории Покраска
сколько нужно материала для покраски, таблица расчета лк
При наличии условий самостоятельная покраска машины обходится автовладельцу значительно дешевле. Один из вопросов, ответ на который хозяин авто пытается найти в первую очередь – сколько краски нужно для покраски автомобиля?

[contents h3]
Что влияет на расход
Расход краски зависит от множества составляющих, самые очевидные из которых – площадь окрашиваемой поверхности и вид лакокрасочного покрытия, планируемого использовать. Для более точного расчета количества придется учитывать множество дополнительных факторов:
- состояние автомобиля, его цвет (если покраска автомобиля осуществляется поверх старого покрытия) или цвет грунтовки;
- выбранная технология окрашивания;
- толщина слоя ЛКМ;
- количество накладываемых слоев;
- марка, тип, состав и цвет краски, которой предстоит окрашивать поверхность, ее укрывистость;
- особенности настройки и работы краскопульта;
- плотность краски, соблюдение пропорций при смешивании компонентов, вязкость состава.
Состав лакокрасочного покрытия и его технические характеристики у разных производителей отличаются. Рекомендуется использовать для работы эмали, лаки, грунтовки, растворители одной марки. В таком случае не будет конфликта составов, следовательно, не потребуется дополнительных расходов на переделку дефектов.
Расход ЛКМ во многом зависит от вязкости рабочей смеси. Покраска слишком густым составом превратит поверхность в апельсиновую корку, которую автолюбители называют шагрень, а слишком жидкий раствор растечется по поверхности подтеками. Для достижения требуемой вязкости пользуются вискозиметром и следуют точным рекомендациям производителей. Причем учитываются все детали – от последовательности смешивания компонентов до соблюдения температурного режима.
Не менее важным фактором является правильная настройка краскопульта (покрасочного пистолета), регулировка давления, подачи воздуха, его достаточный запас для бесперебойной работы и отладка метода распыления. Опыт пользования покрасочным пистолетом уменьшает ошибки и перерасход лакокрасочных материалов.

Снизить расход краски поможет правильная подготовка основания – тщательная грунтовка поверхности детали или всей машины (желательно составом от одного производителя) и мелкозернистое зашкуривание с удалением мельчайших пылевых частиц.
Непосредственно влияет на расход материала укрывистость эмали – способность ЛКМ закрашивать предыдущие слои.
Совет. Если целью покраски является закрасить предыдущие слои с наименьшим расходом материала, то следует учитывать, что наибольшей укрывистостью обладают зеленые и белые цвета, а наименьшей – желтые, красные, синие.
Краска для собственного авто – какую выбрать?
По химическом компонентам, входящим в состав автоэмалей выделяют несколько распространенных видов красок, применять которые возможно в гаражных условиях:
- нитроэмали;
- глифталевые;
- акриловые;
- алкидные.
Нитроэмали имеют ряд недостатков: огнеопасны, недостаточно устойчивы (быстро выцветают), рабочий слой состава очень тонкий, поэтому требуется множественная покраска в несколько слоев. Они постепенно вытесняются более современными материалами.
Глифталевые долго сохнут, причем для высыхания желательна высокая температура, имеют большой период полимеризации – 2–4 недели. Это достаточно неудобно при современном ритме жизни.
Самым распространенным видом, используемым для окрашивания автомобиля в гаражных условиях, остаются акриловые краски. Расход акриловой краски на легковое авто средних размеров составляет 2–3 литра.
Большинство акриловых эмалей двухкомпонентные – для активации состава обязательно добавление отвердителя, а затем снижение вязкости растворителем. Акриловый лак в смесь не добавляется, эмаль сама по себе дает хороший блеск. При желании усилить его лаком, это можно сделать только после полного высыхания слоя акрила, так как скорость испарения у составов разная, и при нанесении по мокрому на поверхности образуются специфические трещины – кракелюр.
Если требуется окрасить автомобиль полностью, то наиболее удобными для работы акриловые эмали, распыляемые краскопультом. Небольшие поверхности удобно окрашивать составом в баллончиках, а для финишного покрытия использовать аэрозольный лак.
При желании использовать алкидные краски для покраски автомобиля следует учесть, что их трудно отполировать, поверхность получится мутная, без блеска. Сохнут алкидные эмали дольше и при более высокой температуре, за время сушки на них собирается много пыли, которую сложно удалить.
Современные автолюбители предпочитают для покраски машин использовать двухслойные краски – состоящие из базы и лака для авто. Понятие двухслойная краска для авто в данном случае обозначает не количество слоев нанесения, а количество покрытий, одно из которых представляет собой базу-пигмент, а второе – обязательный для закрепления базы слой лака. На рынке в достаточном количестве представлена продукция зарубежных производителей (DuPont, NOVOL, Sikkens), банка краски которых стоит дороже, но качество покрытия обеспечивает лучшее.

Расчет расхода лакокрасочных материалов для автомобиля
Расчёт расхода лакокрасочных материалов производится на основании рекомендаций производителя ЛКМ и учета всех факторов, влияющих на их потребление при работе. Покупают неразбавленную краску, в которую добавляется растворитель непосредственно перед началом работ. Количество растворителя (разбавителя) составляет в среднем 20% от количества ЛКМ, но эта величина изменяется в зависимости от вида эмали и того, какой толщины слой нужно нанести.
Усредненные примерные значения расхода ЛКМ при окрашивании автомобиля составляют 200–250 мл краски и столько же лака на 1 поверхности. На средний легковой автомобиль потребуется около 3 л краски, на газель – до 5 литров. Лак расходуется в тех же объемах, что и автомобильная краска. Средние данные для ориентировочного расчета краски представлены в таблице:
Деталь | Расход эмали или лака, мл |
Капот | 400–600 |
Крыло | 150 |
Бампер | 250–300 |
Дверь | 200 |
Крыша | 400 |
Крышка багажника | 350–400 |
Легковой автомобиль средних размеров | 2–3 литра |
Автомобиль типа Газели | 5 литров |
Если требуется окрашивание деталей с двух сторон – внешней и внутренней, количество материалов умножается на два.
Если цвет нового покрытия отличается от прежнего, например, черный автомобиль покрывается белой эмалью, то расход ЛКМ увеличится на 50% за счет нанесения дополнительного перекрывающего слоя.
При работе алкидной эмалью, ее потребуется на 60% больше, чем акриловой.
Использование хорошего краскопульта снижает расход наносимой краски, но требует затрат на его приобретение, регулировку, потребует дополнительного расхода материала на тестирование и выработку навыков работы с пистолетом.
Аэрозольные баллончики 150 г вмещают количество краски, достаточное для покрытия 0,25–0,5 поверхности, следовательно, на 1 понадобится 2–4 баллона с краской.
ПОСМОТРЕТЬ ВИДЕОИНСТРУКЦИЮ
Знание нормы расхода краски поможет сделать правильный расчет материалов, определить стоимость краски для автомобиля, сократить расходы на окрашивание и лакирование.
Эволюция автомобильной краски

Приветствую Вас на блоге kuzov.info!
В этой статье мы рассмотрим историю развития автомобильной краски, современные тенденции её развития и будущие разработки.
Изобретение автомобиля
В 1886 году германским изобретателем Карлом Бенцом было запатентовано его транспортное средство (Benz Motorwagen). Его можно считать первым серийным автомобилем. Более ранние версии транспортных средств мало напоминали современный автомобиль и изготавливались в единичных экземплярах.
Крупномасштабное производство доступных автомобилей было начато Ренсом Олдсом в 1901 году на заводе Oldsmobile в Мичигане. Это была концепция сборочного конвеера, которая в свою очередь была впервые придумана изобретателем Томасом Бланчардом в 1821 году на оружейном заводе. Концепция сборочного конвеера была впоследствии значительно усовершенствована Генри Фордом на своём автомобильном заводе. Другим доступным массовым транспортным средством, который уже больше напоминал современный автомобиль стал Ford Model T, представленный в 1908 году.
1900‑е (Конец 1800‑х – начало 1900‑х)
Началом истории автомобильных покрытий можно считать начало 1900‑х годов, когда, как упоминалось выше, появились первые полноценные автомобили. Форд использовал такой же процесс окрашивания, который применялся при покраске карет. Окрашивание включало 22 последовательных стадии, которые растягивались вплоть до 40 дней для окрашивания всего кузова. Много времени занимала сушка каждого нанесённого слоя краски.

Это были краски, применяемые по дереву, которые наносились кистью и сохли естественным путём. После высыхания краску выравнивали шлифованием, снова наносили слой и снова выравнивали, пока не достигалась нужная толщина. Последний слой также выравнивали шлифовкой и потом полировали, чтобы получить глянцевое покрытие.
Краска тех времён имела низкую износостойкость и низкую защиту от разрушительного действия солнечных лучей. Уже через 2 года эксплуатации были видны следы её разрушения.
Действительно ли автомобили Ford Model T были только чёрного цвета?
«Покупатель может получить автомобиль любого цвета, который пожелает, при условии, что он чёрный» — Генри Форд, 1908.
Первые прототипы и производственные модели Ford имели обозначения буквами от A до T. Они окрашивались в разные цвета. Автомобиль Ford Model T был представлен в 1908 году и до 1913 года покупатели могли выбрать разные цвета кузова, включая чёрный.
Покраска была слабым звеном в инновационном конвейерном процессе Форда.
Компания Ford получила больше заказов на автомобиль Model T, чем она могла выполнить. Генри Фордом было принято решение об упрощении и ускорении производства. Так осталась только одна модель Model T и только один цвет – чёрный. Чёрный был единственным цветом, при котором краска сохла быстро, а скорость была важна для компании Ford из-за большого количества заказов. Использовалась система покраски, которая быстро сохла только при применении чёрного пигмента. В итоге цель была достигнута – было организовано массовое производство, которое привело к удешевлению автомобилей, что сделало их доступными для массового покупателя. Основываясь на данных компании Ford, в 1914 году было сделано 300000 Model T, тогда как конкурентные автопроизводители все вместе изготовили около 280000 машин.

Таким образом, только в чёрный цвет машины Ford красили с 1914 по 1925 год. То есть автомобиль Model T производился в чёрном цвете только 12 лет подряд из общих 19 лет производства этой модели. В другие 7 лет цвета были разные – зелёный, ярко красный, тёмно синий, коричневый, тёмно-бордовый и серый.
Потом, в 1926 и 1927 годах, цвета включали зелёный, светло голубой, коричневый, тёмно-бордовый и чёрный.
1920‑е (изобретение нитроцеллюлозной краски и покрасочного пистолета)
Химики компании DuPont, которые использовали нитроцеллюлозу для производства киноплёнки, обнаружили, что при изменении молярной концентрации NO2 в основе целлюлозы, они получат лак с низкой вязкостью, которым можно будет формировать декоративно-защитное покрытие. Так в 1923 году компания DuPont разработала нитроцеллюлозную краску. В это же время технологии окрашивания автомобилей перешли на использование распыляющего оборудования и стали использовать сушку в камерах. Эти два усовершенствования сократили время нанесения и сушки краски. Время сушки сократилось с нескольких дней до нескольких часов. Нитроцеллюлозная окрасочная система включала множество цветов и предлагала улучшенные свойства для использования с покрасочными пистолетами. Эта система предполагала нанесение 3–4 слоёв для достижения лакокрасочного покрытия с требуемыми свойствами, но имела относительно слабую устойчивость к воздействию химически активных веществ окружающей среды.
лакокрасочного покрытия до нескольких дней. Из-за новой технологии нанесения краски распылением покрытие сразу получалось более ровным и не требовало выравнивания шлифованием.
В 1923, 1924 Oakland (предшественник Pontiac) стал первым автомобилем, покрашенным методом распыления. После этого было сделано много усовершенствований процесса распыления и сушки, но этот шаг стал переломным в производственном процессе окрашивания, значительно повлиявшим на качество и скорость производства.
1930‑е, 1940‑е (появление алкидной краски)
Нитроцеллюлозная краска была очень продуктивной, но финальное покрытие требовало полировки для достижения блеска. Химики-разработчики красок в 1930‑х поставили задачу получить краску с блеском после нанесения, не требующей полировки. В результате была разработана алкидная система окрашивания. Это был первый полимер, разработанный для формирования лакокрасочного покрытия. Он был синтезирован с использованием трёх мономеров (ангидрид фталевой кислоты, глицерин и линолевая кислота). Таким образом, получилось объединить синтетические мономеры и натуральные продукты. Алкидные краски обеспечили отличные свойства плёнки. Они продвигались как краски, специально предназначенные для автомобилей. После сушки в специальных камерах с нагревом алкидные краски формировали очень износостойкую плёнку. Они хорошо противостояли воздействию химикатов и растворителей. Также их преимуществом было более быстрое нанесение, так как для получения нужных свойств требовалось меньшее количество слоёв. Кроме того, алкидные краски обеспечивали больший спектр оттенков, удовлетворяющий запросы потребителей. Однако, недостатком алкидных эмалей было ухудшение декоративных свойств под солнечными лучами. Краска выцветала и мутнела с течением времени.
Так, в течение 1930‑х при окрашивании автомобилей использовались как нитроцеллюлозные, так и алкидные краски. К примеру, компании Chrysler, Ford, Nash, Willy’s и Studebaker использовали алкидные эмали, тогда как General Motors и множество небольших независимых производителей продолжали красить нитроцеллюлозной краской.
В конце Второй Мировой Войны в Европе было запрещено использование некоторых химикатов в производстве. Это сделало некоторые компоненты нитроцеллюлозной краски незаконными.
1950‑е и 1960‑е (появление акриловых красок, изменение способа нанесения грунта)
В 1950‑х, на западе и в Европе, автомобиль стал не просто средством передвижения, а статусной вещью. Это значило, что покрытие кузова должно выглядеть лучше и подчёркивать формы кузова. Компания (Rohm and Haas Co.) разработала новый синтетический полимер акрил. Он стал первым полностью искусственным полимером, который начали использовать при окраске автомобилей. Краска наносилась распылением, после чего сушилась при определённой температуре в специальных камерах.
Акриловые краски имели широкий выбор ярких цветов, а также стали хорошей основой для использования эффекта «металлик». Частицы алюминия энтузиасты-кастомайзеры Америки и Европы добавляли в краску и раньше, а серийно первые блёски в краске появились в 1930‑х годах на таких автомобилях, как Cadillac and Packard, однако, в массовом производстве их стали использовать только после того, как компания «Alcoa» начала производить специальные алюминиевые чешуйки для краски. Эти чешуйки были более яркими, большими и одинаковыми по размеру, чем те, что предлагались другими компаниями раньше. «Металлик» расширял восприятие изгибов кузова. Этот пигмент вывел окраску автомобилей на новый уровень.
Вначале 1950‑х процесс нанесения грунта изменился с распыления на погружение в резервуар, более автоматизированный процесс, но и более опасный из-за испарений большого количества растворителей.
По этой причине, в 1960‑х стали использовать водорастворимые электроосаждаемые грунты с погружением в резервуар, которые более эффективно покрывали кузов. Сначала использовался анодный перенос грунта, потом катодный, обеспечивающий лучшую антикоррозионную защиту при помощи эпоксидной основы. Современный процесс нанесения покрытия электроосаждением усовершенствован и даёт максимально гладкое покрытие.
Акриловые краски доминировали при окрашивании автомобилей на заводе с 1950‑х до 1970‑х годов. Акрил давал отличный финишный слой.
Конец 1970‑х, 1980‑е (появление двухслойного покрытия «база+лак» и водорастворимых красок)
В конце 1970‑х автомобильные производители потребовали у производителей красок лучшей износостойкости лакокрасочных покрытий. Потребитель ожидал, по крайней мере, не менее 5 лет эксплуатации во время которых кузов машины должен выглядеть как новый. В тоже время, агентство по защите окружающей среды начало провозглашать новые правила VOC (volatile organic compound), ограничивающие количество летучих веществ в краске.
Для решения проблемы износоустойчивости покрытия и улучшения декоративных свойств было разработано двухслойное покрытие. Теперь, вместо одного декоративного и одновременно защитного слоя наносилось два разных слоя. Это покрытие включало тонкий базовый слой краски и более толстый слой лака. Базовый слой является пигментным и дающим основной цвет автомобилю, после чего он защищается прозрачным лаком, придающим блеск. В то время такой способ окраски использовался только для дорогих автомобилей. К концу 1980‑х процесс окраски базой и последующим покрытием лаком стал более доступным и стал использоваться более широко.
Эта система имеет ряд преимуществ:
- сокращённое содержание растворителей
- лучшая износостойкость
- возможность использования красок с различными эффектами в базовом слое.
Лак даёт как хорошую защиту, так и отличный блеск. В него добавляли УФ-ингибиторы, чтобы защитить лак и пигменты базы от окисления. Такая система позволила сбалансировать преимущества всех предыдущих красок.
Кроме появления двухслойной системы окрашивания в конце 1970‑х начале 1980‑х произошёл ряд других событий в мире автомобильных покрытий:
- Была разработана система окраски трёхслойным перламутром, которую впервые начала использовать компания Audi. В перламутровых красках металлические частички заменены керамическими кристаллами (слюдой mica), которые не просто отражают свет, но и преломляют его, разделяя на разные цвета. Это придаёт краске не просто блеск, но и глубину цвета, который может изменяться в зависимости от угла обзора. Некоторые цвета могут иметь одну и ту же базовую краску, но в качестве пигмента для придания «эффекта» иметь металлические частички, либо перламутровые. Разница в глубине и мерцании блеска будет заметной, особенно на тёмных цветах.
- Позже производители автомобилей искали краску с улучшенной износостойкостью и более быстрой сушкой. Начали экспериментировать с полиуретановой краской. Она имеет отличные эксплуатационные свойства, однако достаточно дорогая и не широко распространена. Полиуретановую краску по сей день используют некоторые производители.
- В конце 1970‑х стали ожесточаться требования к экологичности красок при процессе окрашивания. Индустрия производства автомобильных красок стала двигаться в сторону снижения летучих органических соединений (растворителей). Начались эксперименты с использованием окрасочных систем на водной основе. Базовая краска на водной основе была впервые представлена на автозаводе Opel в Германии в 1980‑х. В 1990‑х также появились грунты на водной основе.
- В 1970‑х была улучшена антикоррозионная защита кузова за счёт применения электроосаждаемых грунтов (e‑coat). Сначала применялся анодный метод нанесения грунта, а потом более надёжный катодный метод, разработанный компанией PPG. Это значительно улучшило антикоррозионную защиту кузовов автомобилей, что стало прорывом в автомобильных защитных покрытиях.
1980‑е – 1990‑е (порошковое покрытие)
Были приняты новые законы, ограничивающие содержание летучих веществ в краске и способ её распыления. Так стали использоваться уретановые и полиуретановые краски.
В 1970‑х некоторые заводы компаний GM и Ford начали использовать порошковый метод нанесения финишного покрытия. Было сделано несколько тысяч автомобилей с использованием гибридного полиэфирного порошка, но внешний вид и долговечность этих покрытий не смогли конкурировать с акриловыми эмалями горячей сушки, поэтому порошковый метод нанесения финишного слоя не получил продолжения, но остался в качестве метода для нанесения грунта. В 1990‑х был разработан порошковый акриловый лак. Впервые он использовался на заводах Harley Davidson. Далее порошковый акриловый лак применялся на одном из заводов Ford в Детроите с 1996 по 2000. В 1996 году BMW построила линию по нанесению порошкового лака. На данный момент у BMW 5 линий по порошковому методу нанесения лака. По началу, для нанесения порошкового лака использовались краскопульты, но в 2002 они были заменены на специальные порошковые так называемые «колокола», которые дают лучшую скорость переноса материала и уменьшают вероятность появление дефектов.
Конец 80‑х и начало 90‑х принесли быстрые и глобальные изменения в индустрии. Новые экологические законы предписывали содержание и нанесение красок. Были снижено количество растворителей в красках. Объектом интереса для автопроизводителей долгое время было порошковое покрытие. Порошок, содержащий полимер и пигмент наносятся на поверхность без помощи жидкости. Порошок помещается в контейнер с электрическим зарядом, который прикреплён к распылителю. Также заряд подаётся на окрашиваемую деталь. При распылении частицы с зарядом распыляются и плотно притягиваются к металлической детали. Далее окрашенная деталь запекается. Во время нагрева порошок плавится и формирует ровную защитную плёнку. Этот процесс популярен для окраски деталей, используемых под днищем автомобиля и при реставрации, когда требуется высокая износостойкость, но не требуется идеально ровное покрытие.
1990–2000‑е (водорастворимые краски и новый процесс нанесения)
В 1990‑х разработали и стали использовать водорастворимые краски в качестве базы. Первые водорастворимые краски были представлены на заводе Opel в Германии. Главным мотивом использования водорастворимых красок было сокращение летучих веществ в краске и уменьшение вреда экологии. Но это не единственное преимущество использования водорастворимой базы для покраски автомобиля. Благодаря особым свойствам, она обеспечивает улучшенные декоративный внешний вид и улучшенный эффект «металлик». Позже были представлены водорастворимый грунт и лак. Законодательство в Германии поддержало эту технологию.
Современный процесс окрашивания автомобилей
Сегодня процесс окраски автомобилей более стандартизован как никогда раньше. Изменения претерпел способ нанесения краски. Сейчас на высокотехнологичных заводах не требуется участие маляра в процессе окраски кузовов. На заводах краска наносится роботизированными распылителями и сохнет в течение нескольких часов.
Это привело к высшей степени эффективности переноса материала, результатом которого стала 90% эффективность и покрытие без дефектов. Несколько факторов способствовали развитию робототехники для окраски автомобилей. Во-первых, это риск здоровью маляров и большие вложения в безопасное оборудование для маляров. Второй фактор – опасность электростатической техники нанесения краски. Другим фактором было недостаток качества ручной покраски. Специалисты-маляры теперь стали инженерами, которые программируют и запускают роботизированные системы окраски и следят за параметрами окрасочных камер. Современный процесс окрашивания, включая подготовку, занимает не более 8 часов на кузов.
Современный процесс окрашивания состоит из пяти главных этапов и включает:
- Предварительную обработку (очистка металла и формирование подходящей поверхности для хорошей адгезии последующих слоёв).
- Следующий шаг – электроосаждение (electrodeposition (ED)) антикоррозионного защитного слоя.
- Нанесение слоя ПВХ на отдельные детали для антикоррозионной и антигравийной защиты.
- Далее наносится грунт для обеспечения адгезии между поверхностью кузова и базового слоя краски. Грунт также делает поверхность более гладкой и имеет демпфирующие свойства, уменьшающие вероятность сколов при эксплуатации автомобиля.
- В завершение наносятся финишные слои, которые включают базовый слой (краска) с лаком, придающие поверхности декоративные и защитные свойства.
Предварительная обработка
После того, как металлические кузовные компоненты свариваются вместе, кузов автомобиля проходит предварительную многоэтапную подготовку. Она состоит из чистки поверхности кузова, чтобы удалить остатки масел от процесса штампования, а также от остатков сварки. Чистка состоит из процесса последовательного погружения кузова в три ванны (обезжиривание, кондиционирование, фосфатирование). Дополнительно может быть применено погружение в горячую pH9 воду. Предварительная обработка помогает улучшить адгезию грунта к металлу. Фосфатирование улучшает антикоррозионные свойства кузова. Кондиционирование поверхности (также называется активацией) подготавливает поверхность к фосфатированию. Завершающим этапом предварительной подготовки является фосфатирование. Средство для фосфатирования состоит из ортофосфорной кислоты, солей фосфорной кислоты, нитратов, цинка и других вспомогательных компонентов. Кислота протравливает металл. В итоге фосфатирования формируется тонкий плотный слой.
Нанесение финишных слоёв
Далее металл грунтуется, наносится база, потом лак. Некоторые автомобильные производители используют при окрашивании базовые краски на водной основе (в основном в Европе), но лак, в большинстве случаев, применяется обычный.
Вот ещё несколько фактов, которые касаются современной индустрии окрашивания автомобилей.
- Сегодня примерно 1000 новых цветов появляются на рынке каждый год, а общий банк данных за последние 30 лет содержит 25000–40000 цветов. Широко применяются пигменты, придающие «эффекты» краске (алюминиевые чешуйки, слюдяные чешуйки и другие типы пигментов). Возможности дизайна цвета стали неограниченными.
- Современные электроосаждаемые грунты наносятся на кузов при помощи погружения кузова в резервуар с водорастворимым грунтом и покрытие наносится методом катодного электроосаждения. Этот метод гарантирует 100% покрытие всей металлической поверхности грунтом. Грунт имеет эпоксидную основу. Этот метод улучшения антикоррозионной защиты кузова на сегодняшний день остаётся самым лучшим. Хотя электроосаждённый грунт обеспечивает отличную защиту от коррозии, он имеет два недостатка: недостаточно ровную поверхность и плохую светостойкость. Для устранения этих недостатков в 1980‑х были разработаны грунты, которые наносятся поверх электроосаждаемого грунта для улучшения гладкости и улучшения защиты от УФ-разрушения. Эти грунты (Primer-surfacers) обеспечивают защиту от сколов. Комбинация электроосаждаемого грунта и дополнительного выравнивающего грунта обеспечивают хорошую защиту от коррозии и дают ровную поверхность под нанесение базы и лака.
- Современная технология изготовления и нанесения порошкового покрытия значительно улучшена. Оно удовлетворяет требования экологического регулирования. Порошковые покрытия сейчас используются на некоторых заводах для грунтования (к примеру, на заводах BMW), а также некоторыми производителями при процессах лакирования. Порошковый лак является экологически безопасной технологией, так как он не выделяет в окружающую среду какие-либо органические летучие вещества во время нанесения. Кроме того, порошковый лак имеет следующие преимущества: 1. безотходное нанесение (собранный остаток порошка можно снова использовать), 2. нет остатков мусора после нанесения лака, 3. не требуется растворителей для чистки оборудования и камеры (достаточно только пропылесосить), 4. сокращение общего расхода энергии, 5. получается такая же толщина плёнки и внешний вид, как и при использовании жидкого лака.
- Толщина современных плёнок ЛКП меньше, чем 25 лет назад, но защита от коррозии, долговечность цвета и блеска примерно в 2 раза выше. Этому способствовали покрытия наносимые методом катодного электроосаждения и двухслойная система нанесения ЛКП.
- Цвет автомобилей стал очень важным инструментом дизайна. По этой причине тренды оттенков цветов обсуждаются производителями автомобильных красок и автомобильной индустрией вместе.
Ксиралик (Xirallic)
Ксиралик является достаточно новым пигментом, который используется в современных автомобильных красках. Он был разработан и запатентован исследователями компании в японии (Merck KGaA). Этот пигмент характеризуется своим искрящимся эффектом. Ксиралик сделан из пластинок оксида алюминия, покрытых оксидом титана, который даёт сильный эффект блеска с отличным мерцающим поведением.
Матовое покрытие
Матовое покрытие не сильно распространено и обычно бывает серым или чёрным. Иногда это больше сатиновый блеск, чем матовый. Матового лакокрасочного покрытия можно достичь несколькими способами, но в большинстве случаев это достигается высоким содержанием ПВХ в краске или наличием специальной добавки в лак, дающей матовый эффект. Эта краска требует особого ухода, отличающегося от обслуживания обычного глянцевого покрытия.
Краска, меняющая цвет
Пигмент «хамелеон» (ориг. англ. название. ChromaFlair) используется в окрасочных системах при окраске автомобилей. Краска с этим пигментом меняет цвет в зависимости от ресурса света и угла обзора. Эффект достигается отражением и преломлением света от окрашенной поверхности. Краска содержит маленькие тонкие синтетические пластинки, сделанные из алюминия, покрытого фторидом магния, внедрённого в полупрозрачный хром. Алюминий и хром дают краске яркое металлическое искрение, а стеклоподобное покрытие фторида магния действует как преломляющая призма, изменяя цвет поверхности при передвижении наблюдателя.
В Интернете можно найти несколько видеороликов, на которых автомобильная краска может менять свой цвет по нажатию кнопки. Этому явлению предлагаются различные объяснения. Объясняется это как использование специальной «нано краски» (электромагнитная или парамагнитная). Как бы это не называли, базовая идея в том, что краска контролируется магнитными импульсами, которые изменяют малекулярную структуру пигмента краски, заставляя испускать свет на волнах разной длины. Однако, ничего из этого не является правдой. Цвет автомобилей в этих видео меняется в результате цифрового редактирования с использованием программы (Adobe After Effects).
В автомобильной прессе была информация о разработке краске меняющей цвет. К примеру, ещё в ноябре 2007 года было заявлено, что компания Nissan разрабатывает парамагнитную краску, меняющую цвет. Были даны следующие объяснения: высокотехнологичная парамагнитная краска меняет оттенок по нажатию кнопки. Перед покраской машины, металл кузова покрывается частицами оксида железа. Когда электрический ток начинает воздействовать, расстояние между маленькими кристаллами изменяется. Это миниатюрное движение влияет на то, как парамагнитный слой отражает свет, заставляя краску менять цвет, в зависимости от подаваемого напряжения. Но с 2007 года больше не было сообщений от Ниссан о парамагнитной краске.
Недавно компания LitCoat анонсировала создание парамагнитной электролюминисцентной краски, которая может менять цвет, когда контактирует с электрическим зарядом. Однако, на видеоролике компании краска не меняет цвет с одного на другой, а излучает люминесцентное свечение при подаче напряжения.

Парамагнитная краска LitCoat наносится в 2–3 слоя. Можно подпитывать током 1–2‑3 слои одновременно, 2–3 одновременно, 1–2 или 1–3. Эти комбинации будут высвечивать отдельный цвет. Не включен ток – 1 цвет, пропущен ток через 1 слой – 2 цвет, пропущен ток через 2‑ой слой – 3 цвет. Пропущен ток через 1+2 слой – 4 цвет. и т. д. Краска LitCoat наноситься на специальный грунт, который изолирует металлическую поверхность. Такую краску можно смешать с обычной краской, как добавочный пигмент и можно наносить на любую поверхность. После нанесения слоёв парамагнитной краски можно поверх неё нанести любой лак.
Будущие разработки
- В будущем краски продолжат меняться. Главными движущими силами усовершенствования автомобильных красок являются качество, стоимость и экологические нормы. Качество в этом контексте относится к антикоррозионной защите и длительности блеска. Будет улучшаться износостойкость лаков, а также адгезия и цвета красок. Скорость производства также всегда будет движущей силой в развитии окрасочных систем. Даже страховые компании платят за ремонт, основываясь на затраченных нормо-часах, что требует ускорения процессов покраски и использования соответствующих материалов.
- В недалёком будущем автомобильные окрасочные системы будут развиваться и получат следующие усовершенствования:
- УФ-отверждение, лаки стойкие к царапинам. Невероятно быстрое время сушки уже сегодня возможно благодаря использованию в мастерских УФ-катализируемых смол (UV-catalyzed resins). В будущем эта технология будет и дальше развиваться. Стандартные лаки имеют плотность взаимосвязей 8–12 MPa. С УФ-отверждением можно достичь гораздо большей плотности связей частиц лака. Плотность взаимосвязей выше 30 MPa даст хорошую стойкость к царапинам. Высокая плотность взаимосвязей УФ-лаков даст хорошую стойкость к царапинам и воздействию химических элементов. В то время, как обычные лаки для сушки нагреваются до 140 градусов в течение 20 минут, то УФ-отверждаемые лаки могут полностью отвердевать за секунды под воздействием УФ-излучением. Это значительно ускорит общий процесс окраски. Ограничением является то, что не на все места кузова будет попадать прямой УФ-свет, что является причиной не отверждённых зон. Это ограничение привело к развитию комбинированной технологии, позволяющей включать дополнительную реакцию отверждения в местах без воздействия УФ-света. Когда видимые области экстерьера автомобиля достигают полной полимеризации под воздействием УФ-света и дополнительной хим. реакции, области интерьера, куда свет не попадает, будут полимеризоваться за счёт химической реакции с катализатором.
- Будут распространяться водорастворимые грунты и лаки как при окраске новых автомобилей, так и при ремонте аварийных машин.
- Процесс окраски без грунта. Базовый слой обычно наносится в две стадии. Для безгрунтовой технологии изоцианат с добавками будет добавляться на первой стадии нанесения краски. Этот активатор с добавками будет модифицировать характеристики базового слоя так, что он будет выступать в качестве грунта. Это ускорит процесс окрашивания и сократит количество используемого материала.
- Одно из новых направлений – разработка и использование умных покрытий (smart coatings), которые могут значительно улучшить износостойкость поверхности и добавить дополнительные функции и свойства, такие как супер гидрофобность, олеофобность (отталкивает жидкости на основе масел), самоочищение, самовосстановление.
- Самовосстановление может быть достигнуто применением полимеров с «памятью» формы, которая активируется воздействием температуры и влажности или УФ-излучением. Как конкретный пример можно привести использование в составе лакокрасочных материалов специальной монтмориллонитовой глины, которая имеет способность сильно разбухать под воздействием влаги.
- Лаки стойкие к царапинам. В последние годы производители лакокрасочных материалов разрабатывают и тестируют лаки, стойкие к появлению царапин. Царапины особенно заметны на автомобилях с тёмными оттенками. Одна из концепций для получения лака стойкого к царапинам базируется на внедрении твёрдых нано частиц в гибкую матрицу полимера.
[adsp-pro‑4]
Печатать статью
Ещё интересные статьи:
Технология покраски автомобиля: металлик акрил лак
Лакокрасочное покрытие современного автомобиля способно прослужить более 10 лет при аккуратной эксплуатации со стороны хозяина. Однако даже на стоянке нерадивые соседи могут поцарапать кузовной элемент или оставить на нем вмятину. А когда возраст машины перевалит отметку 10 лет, то по всему кузову начнут появляться очаги коррозии. После всех подготовительных этапов наступит очередь самой ответственной операции — нанесение автоэмали. При выполнении этой работы должна соблюдаться определенная технология покраски автомобиля.
Подготовка места для окрашивания автомобиля
Многие начинающие автомаляры не уделяют внимания такому важному моменту, как выбор места для покраски. Здесь есть несколько вариантов.
- Даже опытные мастера любят работать на открытом воздухе. Это объясняется отличным освещением и прекрасной естественной вентиляцией на улице. Однако в течение года можно насчитать не так уж и много дней, когда наблюдается безветренная сухая погода. Покраску лучше производить рано утром, когда солнце еще не активно и рядом не проносятся автомобили и мотоциклы.
- Более надежным местом для работ с краской является гараж. Однако он должен соответствовать целому ряду требований. В первую очередь размеры строения должны быть сопоставимы с величиной авто. Для небольшой легковушки достаточно стандартного помещения длиной 6 м при ширине 4 м. Необходимо позаботиться о хорошем освещении. Много времени придется потратить, чтобы убрать из гаража все лишнее и произвести генеральную уборку. Важно не только удалить пыль с пола, стен и потолка, но и уничтожить всех насекомых. Непосредственно перед покраской помещение увлажняется. В качестве альтернативы генеральной уборке может стать полное укрытие стен и потолка полиэтиленовой пленкой при помощи скотча.
Процессу окрашивания
Технология покраски автомобиля зависит в основном от вида выбранной эмали, а также от величины обрабатываемой поверхности. Если автовладелец не достаточно требовательно относится к качеству лакокрасочного покрытия своего автомобиля, то он может воспользоваться аэрозольным баллончиком для обработки небольших участков. В этом случае следует изучить инструкцию по применению от производителя краски и действовать согласно описанной технологии.
Когда требуется высокое качество кузовного ремонта, то без краскопульта и компрессора не обойтись. Несмотря на некоторые отличия в нанесении разных видов краски для машины, необходимо выделить некоторые общие подходы к операции окрашивания.
- Чтобы качественно нанести автомобильную эмаль на кузов, опытные маляры рекомендуют использовать краскопульт с соплом №1,4.
- Давление, которое компрессор выдает на пистолет, должно находиться в диапазоне 2,5-3 атм.
- Во время окрашивания автолюбитель должен держать краскопульт на расстоянии 15-20 см от поверхности обрабатываемой детали.
- Процесс нанесения краски состоит из формирования 2-3 слоев. Важно не перестараться с толщиной слоя, чтобы не образовались наплывы и подтеки. Время сушки каждого слоя краски должно составлять не менее 15-20 минут. Чем выше температура воздуха, тем быстрее испаряется растворитель и высыхает слой краски.
Окончательным этапом покраски станет полирование затвердевшего лакокрасочного материала.
Разновидности автомобильных эмалей
В настоящее время при покраске автомобилей применяются два типа эмалей.
- Акриловая краска состоит из цветного пигмента, растворителя и связующего компонента.
- Автоэмаль металлик имеет в своем составе такой важный дополнительный пигмент, как алюминиевая пудра.
В зависимости от выбора типа краски применяется соответствующая технология покраски автомобиля. Чтобы выбрать акрил или металлик, необходимо провести простой тест на лакокрасочном покрытии машины. Для этого необходимо смочить салфетку растворителем и потереть в каком-нибудь незаметном месте. Если на салфетке останутся следы краски, то кузов покрашен акриловой краской. А когда салфетка останется чистой, то верхний слой является лаком, что характерно для металлика.
Покраска кузова акриловой краской
У профессиональных маляров используется трехслойная технология покраски акрилом.
- Первый слой является основой для всего покрытия. Он делается самым тонким.
- Второй слой наносится особенно тщательно, он должен полностью укрыть грунтовку и шпатлевку.
- При нанесении финишного слоя краска немного разбавляется. Его задача довести окрашиваемую поверхность до идеального состояния.
Акриловую краску можно покрывать лаком, благодаря чему увеличивается глубина цвета, а также несколько улучшается качество покрытия. Однако сначала необходимо дождаться полного затвердения акрила, после чего краску обрабатывают мелкой наждачной бумагой.
Особенности покраски машины металликом
Не так давно стала особенно популярной краска для автомобилей под названием металлик. Она обладает эффектным внешним видом, особенно под лучами солнца. Сегодня можно встретить три вида автоэмали из категории металлик.
- Однослойный вид не пользуется особым спросом у кузовщиков из-за сложностей с получением качественного покрытия.
- Самым массовым типом металлика является двухслойный материал. Технология покраски заключается в последовательном нанесении базового слоя и лака. При таком способе окрашивания металлик хорошо ложится на слой грунта и быстро высыхает.
- Трехслойную краску автолюбители выбирают тогда, когда хочется создать лакокрасочное покрытие со сложными эффектами. Например, взглянув под одним углом, можно отчетливо увидеть темно-синий цвет. А когда направление при осмотре меняется, то появляются оттенки зеленого цвета.
Нанесение базового слоя
Работа начинается с добавления растворителя в базу. После растворения сразу же необходимо приступать к распылению материала. При первом окрашивании могут возникать полосы и пятна, этого не нужно бояться. Второй слой базовой краски сгладит все шероховатости и непрокрасы. Перед вторичным окрашиванием важно дать первому слою подсохнуть в течение 30 мин. Когда растворитель испарится, слой станет матовым. Ускорять процесс сушки при помощи обдува сжатым воздухом категорически не допускается. Иначе металлические частички могут погрузиться в базовый слой неправильно.
Не рекомендуется оставлять базовый слой на длительную сушку, например, на целую ночь. Это может привести к ухудшению сцепляемости (адгезии), после чего лак может «вспучиться» после высыхания. Поэтому следует ответственно отнестись к той инструкции, которая разработана производителем металлика, и четко выдержать временной интервал перед нанесением лака на базу.
Лакирование
Технология покраски автомобиля эмалью металлик предусматривает подготовку лака перед нанесением. В инструкции указаны пропорции растворителя и закрепителя, которые необходимо добавить непосредственно перед лакированием. Чаще всего лак наносится в 2 или 3 слоя.
При нанесении лака важно не допускать образования потеков или наплывов. Лучше укладывать тонкий слой, а затем после непродолжительной сушки распылять следующую порцию лака. В противном случае придется аккуратно снимать высохший слой и повторно его наносить.
Специалисты обычно проверяют степень высыхания лака прикосновением к покрытию. Если поверхность липкая, но при этом не остается на пальце, то можно формировать следующий слой.
Получить качественное лакокрасочное покрытие на кузове своего автомобиля можно только при выполнении всех технологических операций. При недостаточной внимательности или аккуратности образуются дефекты, которые не сможет устранить полировка. Придется полностью счищать новую краску и повторять все этапы. И только с опытом выработается ответственный подход к работе, что приведет к получению идеального покрытия.
Сколько нужно краски для покраски автомобиля?

Нельзя точно сказать, сколько краски будет затрачено на покраску автомобиля, но есть основные принципы, которые помогут понять расход краски при окрашивании автомобильного кузова.
На количество краски влияет:
- Размер машины
- Цвет наносимой краски и исходный цвет кузова
- Качество краски
- Тип краскопульта
- Опыт маляра
Давайте рассмотрим подробнее каждый пункт.
Размер машины
Конечно же, чем больше машина, тем больше краски потребуется, чтобы её покрасить.
К примеру, чтобы покрасить маленькую малолитражку потребуется менее 2 литров неразведённой краски, тогда как на окрашивание внедорожника, имеющего большую площадь кузова, и краски потребуется больше. Нужно также учитывать, будут ли окрашиваться проёмы. Это также увеличит расход краски.
Цвет наносимой краски и исходный цвет кузова
Количество краски необходимое для покраски автомобиля зависит и от того, каким цветом будет окрашиваться машина и какой исходный цвет имеет окрашиваемая поверхность. Если панель кузова имеет цвет контрастный распыляемому, то краски, соответственно, уйдёт больше. Такие цвета, как жёлтый, красный, синий являются слабоукрывистыми, поэтому такой краски может потребоваться большее количество, чтобы перекрыть исходный цвет. Если краска слабоукрывистая, то необходимо нанести большее количество слоёв для окрашивания подложки. К примеру, при покраске краской красного и жёлтого цветов может потребоваться до 10 и более слоёв.
Хорошей укрывистостью обладают такие цвета, как чёрный, белый, ярко-зелёный.
Если машину перекрашивают из-за многочисленных мелких дефектов и царапин, которые сошлифуются во время подготовки кузова к покраске, то краски уйдёт меньше, чем при смене цвета автомобиля.
Цвет подложки будет влиять на конечный оттенок краски.
Примечание: Укрывистость — это способность краски при распылении полностью перекрывать цвет поверхности, то есть закрывать распыляемым цветом цвет подложки. Таким образом, чем краска более укрывистая, тем потребуется меньшее её количество, чтобы покрасить деталь.
Качество краски
Краска разных производителей может иметь разный состав и, соответственно, разную укрывную способность.
Качественная укрывистая краска может перекрыть подложку в 2–3 слоя.
Тип краскопульта
На расход краски значительно влияет устройство краскопульта. Краскопульты HVLP имеют высокий процент переноса лакокрасочного материала на окрашиваемую поверхность. У качественных краскопультов системы HVLP этот процент составляет не менее 75%. При окрашивании такими краскопультами краска по максимуму попадает на деталь, а не летит по сторонам.
По личному опыту могу сказать, что когда беру качественную краску в количестве, рекомендуемом для покраски нужных мне деталей, и краска часто остаётся (иногда более половины). Крашу я краскопультом Iwata W‑101, приобретённым у официального представителя в России. На собственном опыте убеждаюсь, что качественный экономичный покрасочный пистолет значительно сокращает расход краски.
Опыт маляра
Количество краски, которую потребуется для окрашивания кузова автомобиля зависит также и от профессионализма автомаляра. Опытный маляр правильно настроит покрасочный пистолет и правильно разведёт краску. Краска должна наноситься не в виде пыли, а попадая на поверхность, хорошо растекаться. Разумнее будет сначала закрасить ремонтные области и заменённые панели кузова, имеющие цвет, отличающийся от цвета остального кузова. Далее уже можно переходить к поэтапному окрашиванию всех кузовных деталей.
Базовая краска + лак
Если автомобиль будет окрашиваться краской, требующей дальнейшего покрытия лаком, то лака может потребоваться больше, чем базовой краски. Лаком необходимо создать определённую толщину, так как он является защитным покрытием. К примеру, если на окраску кузова уйдёт порядка 2 литров базовой краски, то лака может потребоваться 3 – 3.5 литра. Даже если лака уйдёт меньшее количество, лучше его брать с запасом и разводить не весь сразу, а по мере расхода. Оставшийся, не разведённый лак пригодится в дальнейшем при покраске любой машины.
Вообще, количество лака зависит от площади, которая будет лакироваться, а не от количества базовой краски. Количество краски и лака могут и совпадать.
Расход краски на одну деталь
На одну кузовную панель расходуется от 100 до 300 грамм неразбавленной краски. Бампера, капот и крыша автомобиля по площади больше остальных деталей кузова и краски на них уходит до 2 раз больше.
Нужно учитывать то, что некоторые детали должны быть окрашены с двух сторон (капот или крышка багажника).
Количество краски, необходимое на окраску всего автомобиля
При экономичном расходовании краски, на весь автомобиль может понадобиться от 2‑х кг краски. Лака нужно примерно такое же количество.
В основном 2–2.5 кг неразведённой краски достаточно, чтобы покрасить четырёхдверный седан. Так как базовая краска разводится 1 к 1 (1 литр краски смешивается с 1 литром разбавителя), то разведённой краски получится в два раза больше.
Если машину нужно покрасить вместе со всеми проёмами, то потребуется краски на 0.5 – 1 кг больше. Так как базовая краска обычно разводится 1 к 1, то количество разведённой для распыления краски будет в 2 раза больше.
Советы:
- Нужно всегда покупать краски и лака больше, чем может потребоваться. Остаток можно оставить на хранение до следующего ремонта. Остатки базовой краски можно сохранить, плотно закрыв в таре. Она не содержит отвердителя, и будет храниться достаточно долго. Даже если спустя некоторое время краска загустеет, её всегда можно развести разбавителем. Перед лакированием, нужно развести половину купленного лака и при необходимости развести дополнительное количество лака.
- Необходимо помнить, что базовая краска и акриловая двухкомпонентная разводятся разными разбавителями. Если базовую краску (требующую последующего лакирования) разбавить универсальным акриловым разбавителем, то при покраске могут возникнуть дефекты, в особенности, при покраске красками с эффектом «металлик» и «перламутр».
[adsp-pro‑4]
Печатать статью
Ещё интересные статьи:
Технология покраски автомобиля
Современная технология окраски автомобиля имеет несколько разновидностей, а выбор конкретного варианта зависит от масштаба выполняемых работ, условий, в которых они проводятся, применяемых материалов. По сути, отличия между разными способами невелики и касаются тех или иных тонкостей. Исключение составляет заводская технология покраски автомобиля, при котором покрытие наносится на кузов путем его окунания в ванну с материалом. При этом для лучшего прилипания на корпус и краску может подаваться электрический заряд противоположной полярности. Здесь мы рассмотрим технологию покраски кузова автомобиля в специализированных ремонтных мастерских.
Подготовительный этап
Как правило, владельцы авто решаются на покраску уже тогда, когда на поверхность проступают следы коррозии металла. Поэтому технология подготовки к покраске автомобиля обязательно предусматривает удаление ржавчины. Сделать это можно двумя способами – химической или механической обработкой. Последняя, в свою очередь, подразделяется на ручную и автоматизированную. Быстрее и надежнее всего устранить ржавчину позволяет пескоструйная обработка. Однако ее применение сегодня достаточно ограничено как дороговизной оборудования, так и особенностями метода. При очистке поверхности металла образуется большое количество пыли, перемешанной с абразивом. Эту массу нужно собрать вручную или с помощью дорогостоящего промышленного пылесоса.
Чаще всего металл зачищают вручную (при небольшой площади поврежденного участка), дрелью с насадкой или шлифмашинкой. При этом используют наждачную бумагу зернистостью Р80-Р240. Слишком мелкую «шкурку» применять не следует. После обработки поверхность металла должна быть достаточно шершавой, чтобы на нее хорошо «легла» грунтовка.
Если коррозия проникла глубоко в толщу металла, то шлифовка не позволит полностью избавиться от ржавчины. В этом случае потребуется применить химический состав на основе кислоты. Продаются такие растворы под названием «преобразователь ржавчины».Следует помнить, что после достижения желаемого результата место обработки необходимо тщательно промыть чистой водой, высушить и сразу переходить к следующему этапу.
Грунтование и шпатлевка
Очищенный от глубокой коррозии участок кузова автомобиля лучше сразу покрыть кислой грунтовкой. Она создаст тонкую (10-15 мкм) пленку, которая препятствует проникновению влаги к металлу в случае появления микротрещин в лакокрасочном покрытии. Если перед покраской требуется восстановить профиль поверхности при помощи шпатлевки, то на кислый следует нанести еще один грунт – акриловый.
Если с ржавчиной особых проблем не было, и ее тонкий слой легко удалился шлифованием, то шпатлевку можно наносить прямо на металл. Для этого ее нужно сначала приготовить, смешав основу с отвердителем. Брать следует такое количество материала, которое будет использовано в течение 5-10 минут. После этого происходит полимеризация, и шпатлевка теряет пластичность. При смешивании шпатлевки и отвердителя должно быть исключено образование в толще материала воздушных пузырьков. Их наличие может стать причиной появления ямок при шлифовке перед покраской.
Мастера, профессионально занимающиеся кузовными работами, знают, что шпатлевка при высыхании дает усадку, поэтому наносить ее лучше несколькими тонкими (до 1,5 мм) слоями, а не одним толстым. При этом следует помнить, что обрабатывать зашпатлеванный участок шкуркой можно начинать через 30 минут, а для укладки еще одного слоя лучше подождать пару часов до полного отвердевания материала.
Шлифовка
Чтобы добиться нужного профиля обрабатываемого участка, применяют сухую или влажную шлифовку. Здесь необходимо учитывать, что мокрый метод не подходит для работы с полиэфирными шпатлевками, поскольку они обладают высокой гигроскопичностью. Такие составы шлифуются только сухим способом, при этом обязательно нужно позаботиться о защите глаз и органов дыхания, надев очки и респиратор.
Для достижения желаемого результата рекомендуется производить шлифовку в три захода. При первом используется шкурка Р80 с крупным зерном. Участки небольшой площади шлифуют с применением резинового или войлочного бруска, обернутого наждачной бумагой. Для формирования сложного профиля лучше подготовить брусок соответствующей формы. Удаление шпатлевки производится возвратно-поступательными движениями, совершаемыми в одном направлении.
Когда профиль почти сформирован, наждачную бумагу меняют на Р180 и меняют направление движения бруска на 90°. Работу продолжают, пока не будет достигнута нужная форма. Затем берут шкурку Р240-Р400 (в зависимости от необходимой гладкости поверхности) и «доводят» участок.
Убедиться, что работа выполнена хорошо, помогают проявочные порошки. Если после их нанесения выявляются глубокие царапины и сколы, потребуется повторить шпатлевку и шлифовку.
Грунтовка
Назначение грунта – обеспечить надежное сцепление краски с поверхностью. Кроме того, на данном этапе можно увидеть оставшиеся дефекты и устранить их, не тратя дорогостоящую краску.
Грунт наносится в 2-3 слоя равными полосами. При этом руководствуются правилом, что следующая полоса должна перекрывать предыдущую примерно наполовину. Цвет грунта выбирают исходя из колера краски.
Нанесение основного слоя краски
В большинстве случаев технология покраски автомобиля предусматривает нанесение двух слоев – базового и финишного, в роли которого выступает лак, стойкий к атмосферным и абразивным воздействиям, возникающим из-за присутствия в воздухе пыли. Из этого правила существуют исключения. Так, технология покраски автомобиля акриловой краской не предполагает применение лака. Впрочем, некоторые мастера все-таки используют его для достижения лучшего блеска.
Техника покраски автомобиля заключается в нанесении 3-х слоев без разводов и подтеков. Первый делается тонким – это нужно для обеспечения хорошего сцепления с грунтом. Второй – основной, самый толстый. Именно этот слой отвечает за ровный, однотонный цвет поверхности. Третий проход выполняется жидкой краской. Финальный тонкий слой обеспечивает глянец.
Нанесение лака
В отличие от акрила, технология покраски автомобиля металликом предусматривает обязательное нанесение слоя 2-3 слоев лака.
Полировка
Финишная полировка позволяет устранить мелкие дефекты: небольшие подтеки лака, случайно попавшие частицы пыли и пр. Именно после этого этапа можно считать окраску автомобиля законченной.
Оставить ответ